automatica 2025 – New type of machining robot closes the gap between classic industrial robots and machine tools
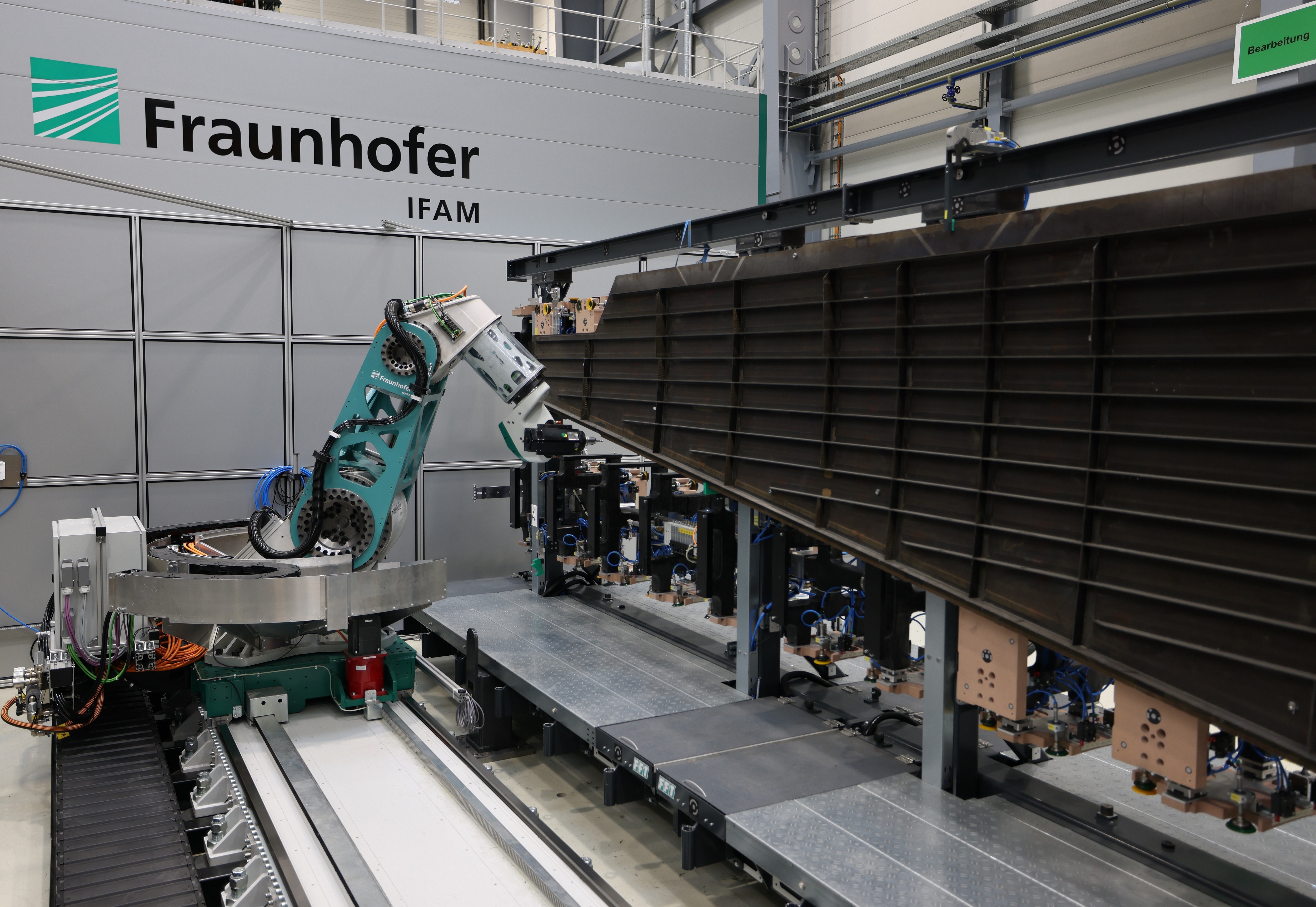
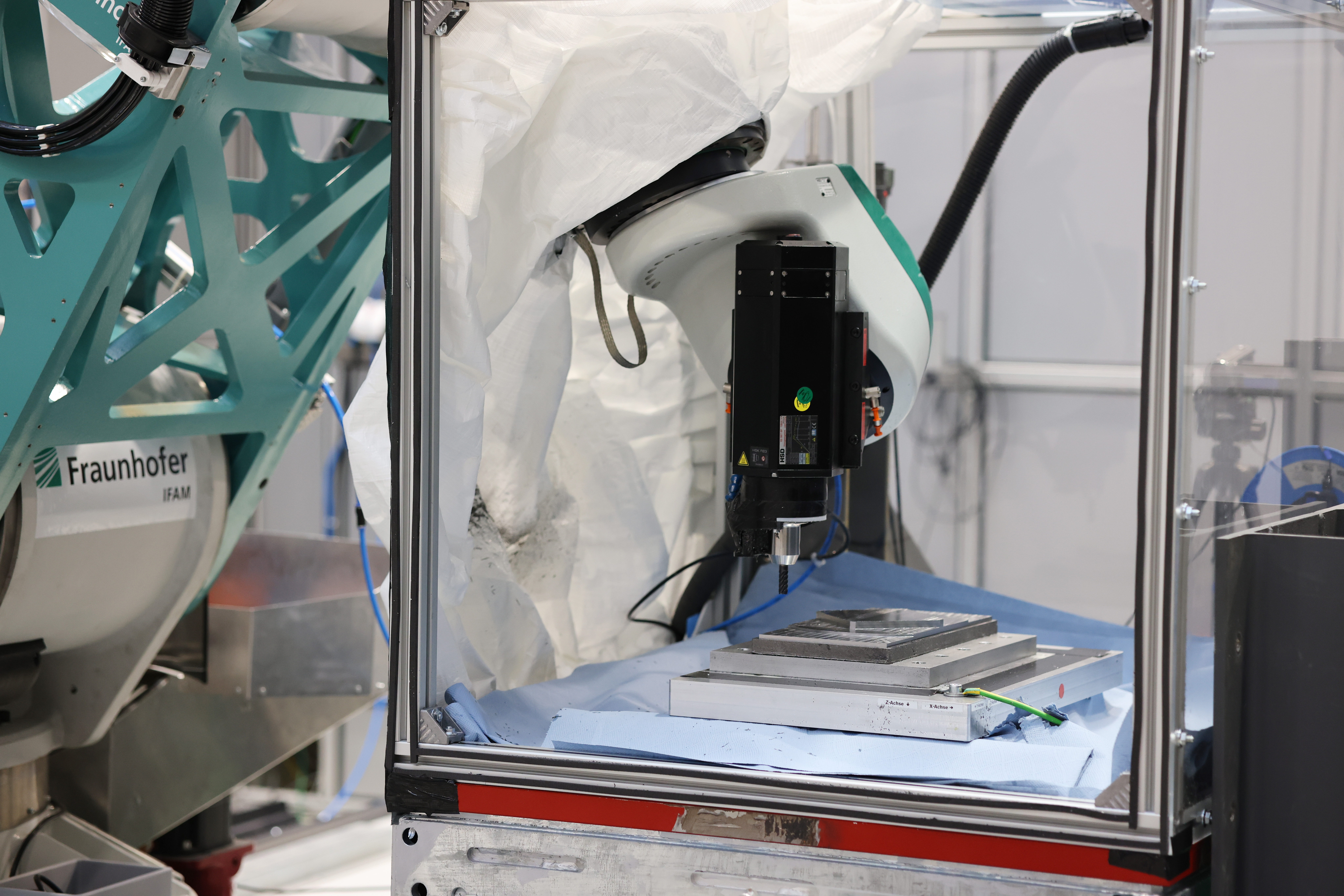
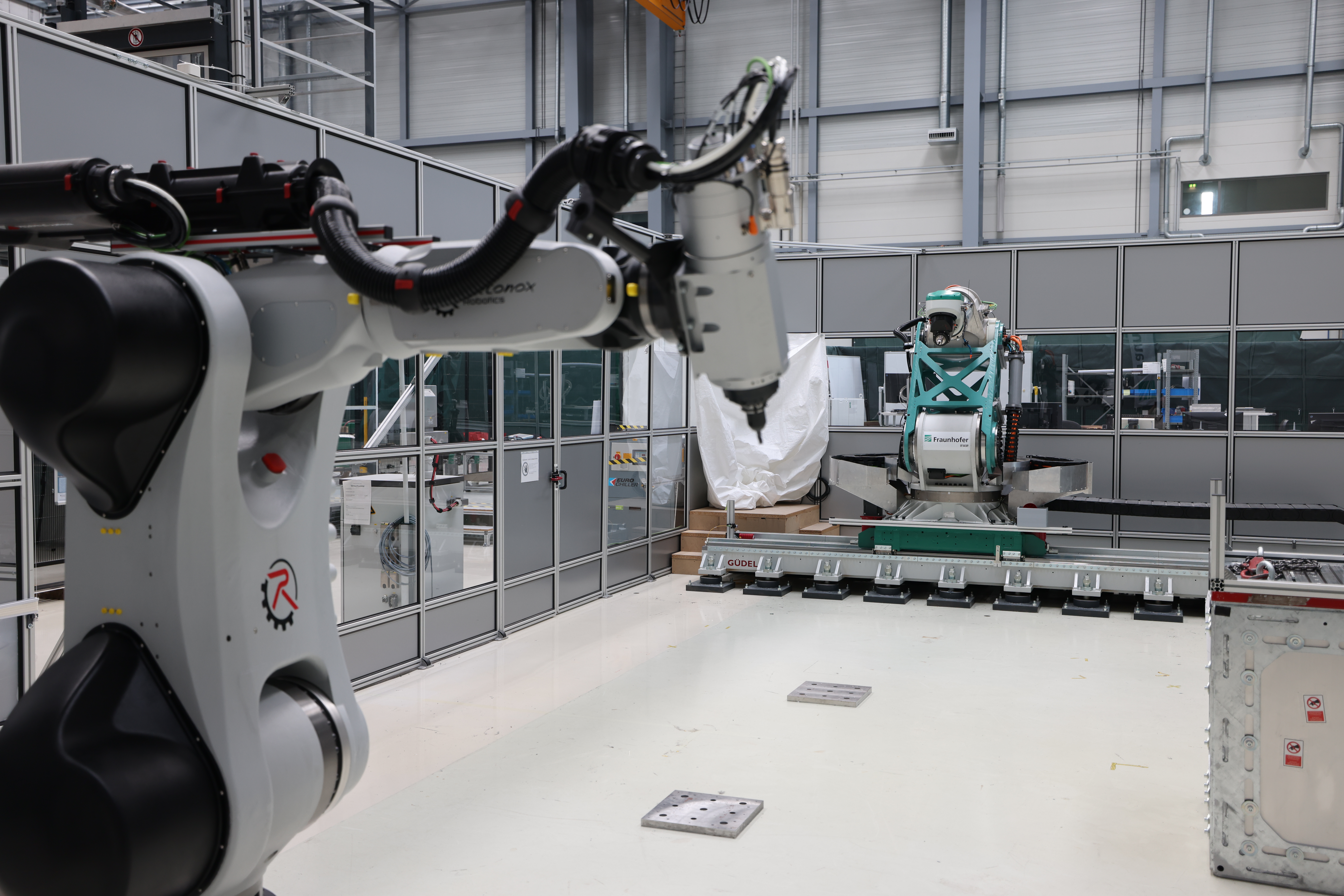
Download
Figure 1: The newly developed flexible milling kinematics on a linear axis machines a CFRP vertical tail plane of an aircraft on a 1:1 scale with high precision.
© Fraunhofer IFAM
Figure 2: The successful high-precision machining of a steel part shows that the machining robot on the linear axis is able to close the gap between industrial robots and machine tools.
© Fraunhofer IFAM
Download
Figure 3: Technology transfer to industrial applications: In the background the flexible milling kinematics developed at Fraunhofer IFAM, in the foreground the jointly developed product solution from autonox Robotics.
© Fraunhofer IFAM