JEC Composites Innovation Award 2025 for the Multi Functional Fuselage Demonstrator – MFFD
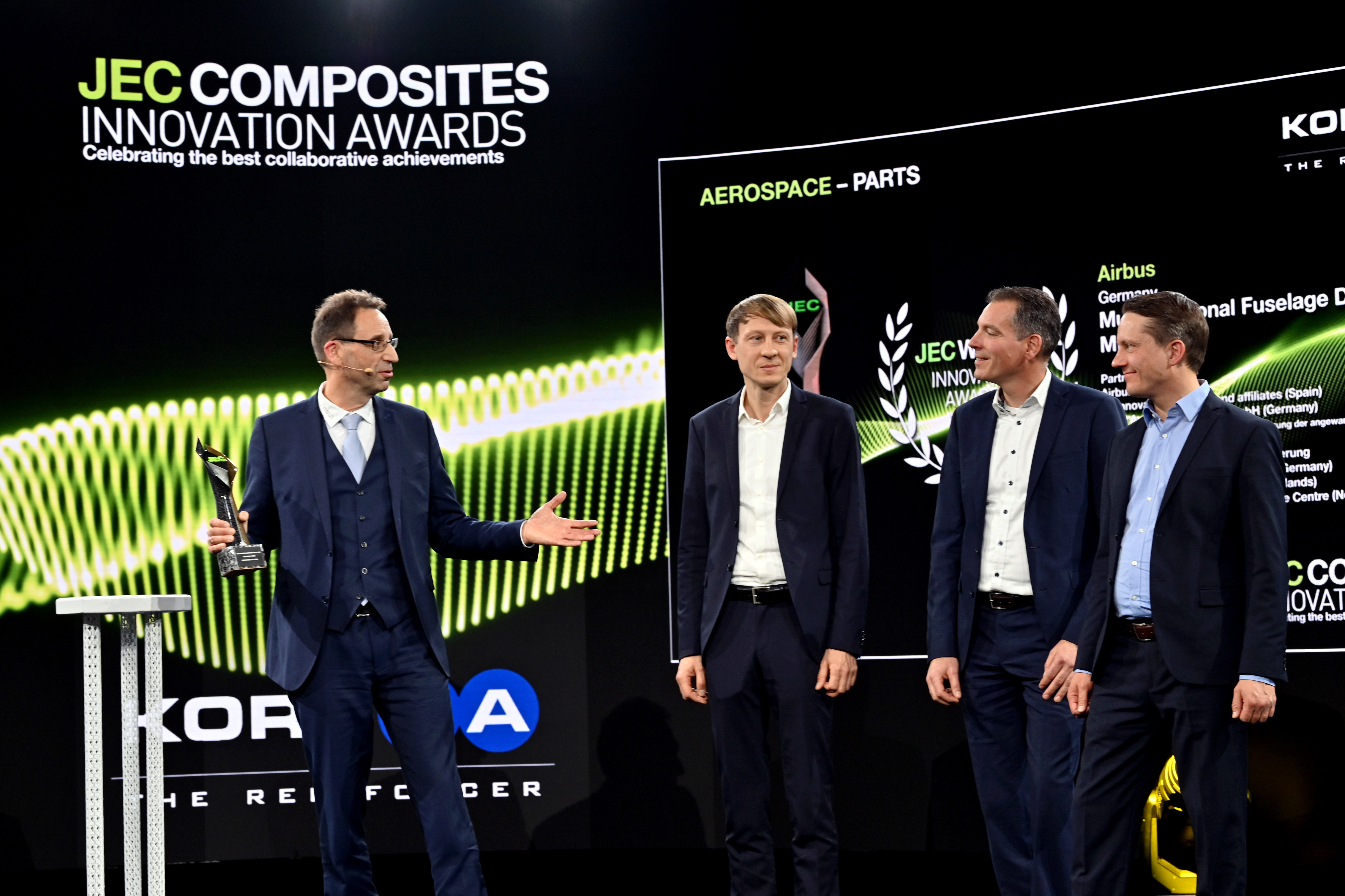
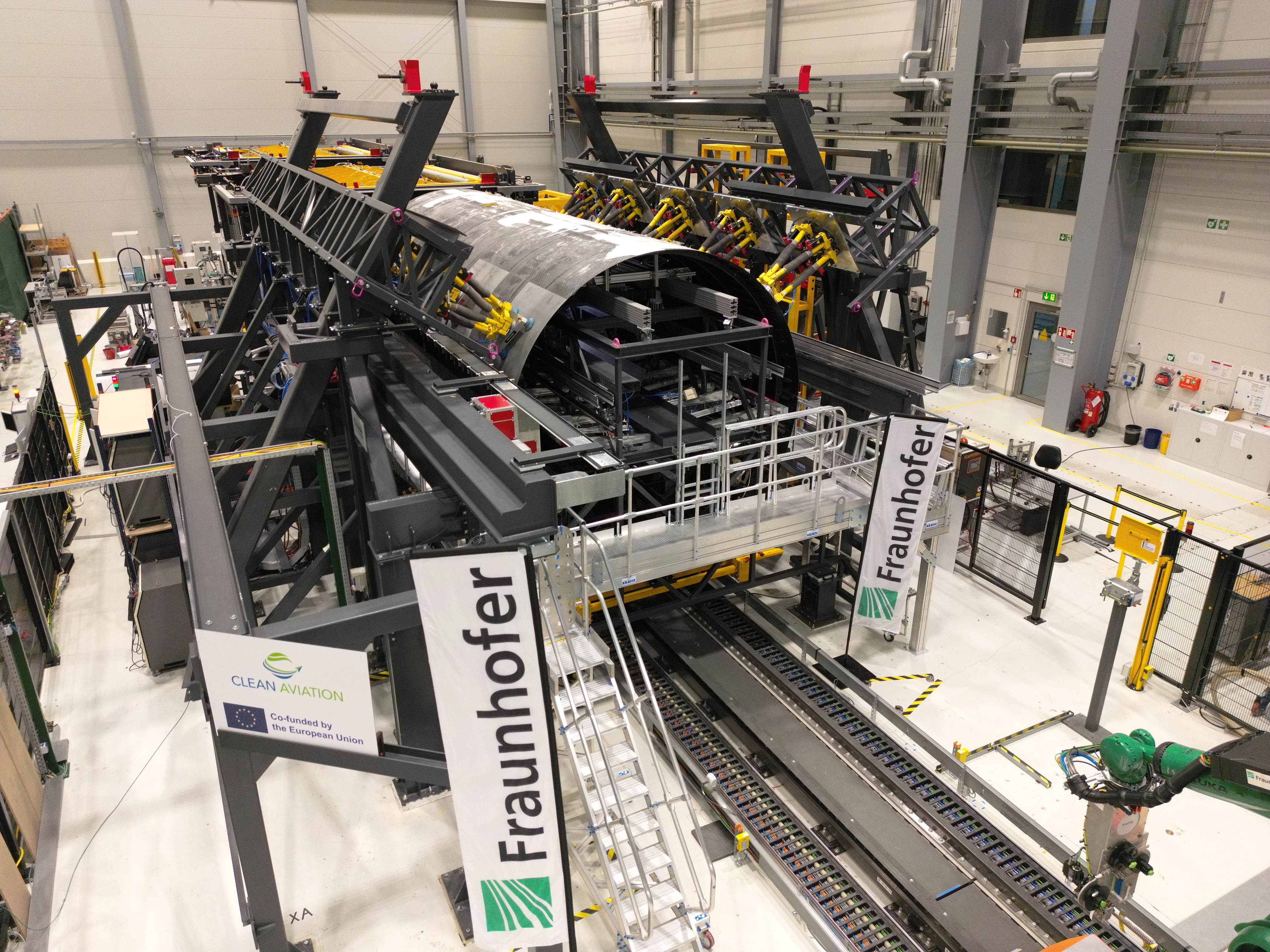
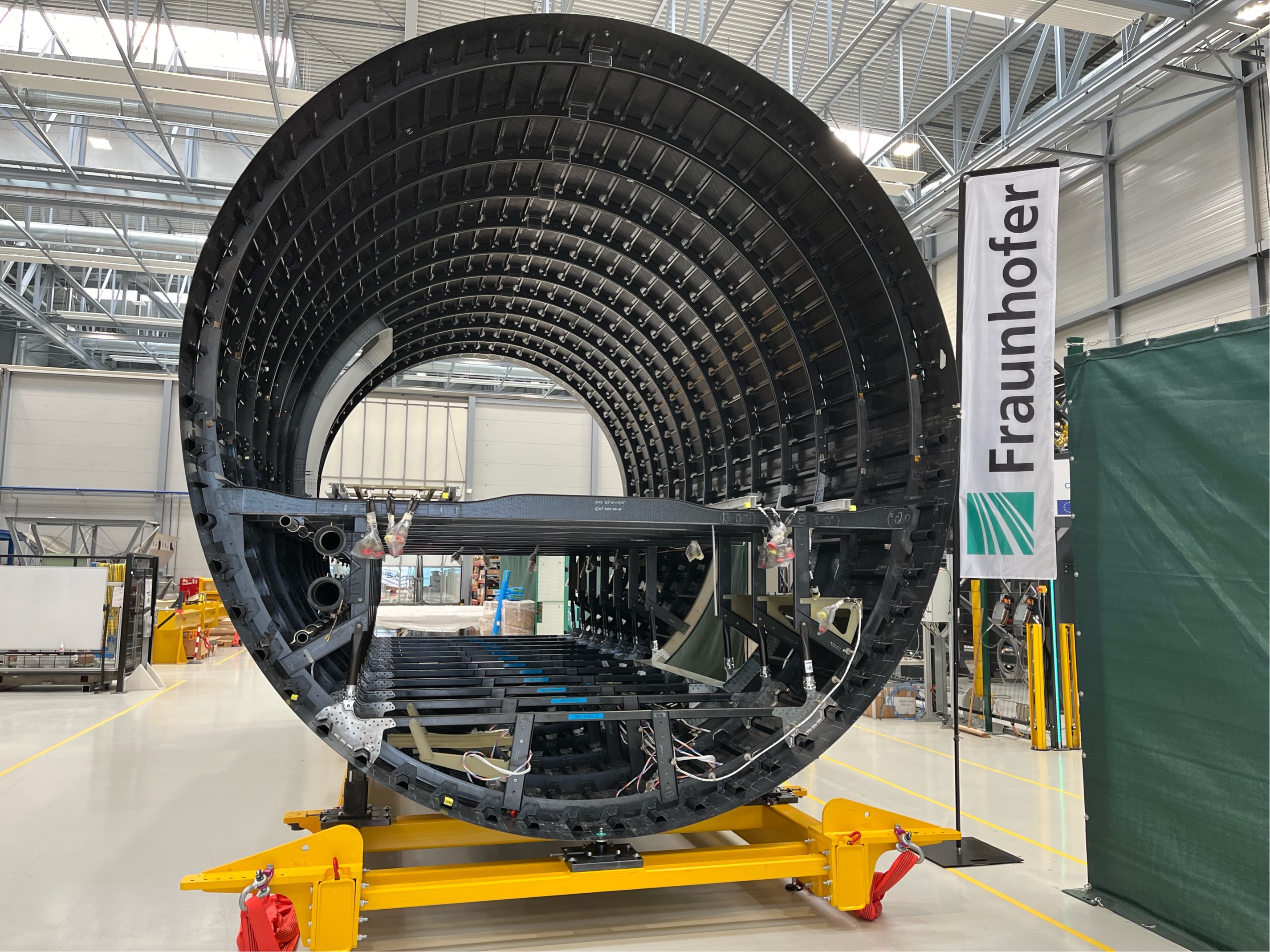
Demonstration of an automation-compatible thermoplastic construction method for aircraft fuselages receives award in Paris
The “Multi Functional Fuselage Demonstrator” (“MFFD”), which was developed in the European Clean Sky 2/Clean Aviation program with the substantial involvement of the Fraunhofer-Gesellschaft, was honored with the “JEC Composites Innovation Award 2025” in the “Aerospace – Parts” category on January 13, 2025, in Paris for its contribution to achieving the goals of future high-rate production and sustainable flight. Airbus, as overall coordinator, applied for the prestigious award on behalf of the approximately 40 international project partners involved.
Thermoplastic construction for high-rate production and weight reduction
The Fraunhofer-Gesellschaft, in collaboration with partners in the Clean Sky 2/Clean Aviation project “Large Passenger Aircraft” (“LPA”), has succeeded in demonstrating for the first time worldwide that the automation-compatible thermoplastic construction method for aircraft fuselages leads to both an increase in production efficiency for high-rate production and a significant reduction in weight, which enables a decrease in CO2 emissions of up to 540 kg per flight. The 10 percent weight reduction and 10 percent cost savings in production achieved in the project are far from exploiting the full potential of the combination of the new design with automated production.
Automated assembly and joining processes of pre-integrated structural and system components
The Fraunhofer-Gesellschaft's contributions included the automation of the assembly of a full scale upper shell with a corresponding lower shell to form the 8-meter-long fuselage section of the “MFFD” with a diameter of 4 meters as well as the development of the laser welding and gap filling processes used for thermoplastic CFRP joints.
Particular challenges in automation were the very high accuracy requirements despite the component sizes as well as the management of the high joining forces combined with limited accessibility. These limitations inside the fuselage resulted from the pioneering approach of an almost complete pre-integration of the two 180° shells with structural and system components. Compared to the current method of equipping the cabin and cargo areas after the fuselage has been closed, it offers considerable advantages for automated, high-rate production.
Joining thermoplastics by welding
In order to avoid carbon fiber-containing dust, various welding processes were already used during shell finishing instead of the usual drilling and riveting processes, which was also the reason for the choice of the new thermoplastic CFRP materials.
As a result, the automation of the fuselage section assembly was characterized by the precise positioning of the two half shells in relation to each other and the individual geometry optimization of the upper shell. This ensured that the joining areas of the longitudinal seams on the fuselage were reliably below the required tolerances permitted for the welding processes. The high joining forces generated externally during the welding process were absorbed and dissipated inside the fuselage by automated pressure units to prevent damage to the CFRP structure.
Perfect joints could only be guaranteed if the partly parallel and partly sequential running sub-processes of positioning, supplying additional joining elements, heating, gap filling and pressing were precisely coordinated and monitored in terms of time and space by a central control system. Accordingly, the two welding processes used, CO2 laser welding for one longitudinal seam and ultrasonic welding for the other, were each expected to achieve a high level of perfection.
Potentials for aircraft manufacturing and ...
The results obtained open up a whole range of new options for future aircraft production, primarily in the use of lightweight, thermoplastic CFRP materials in conjunction with joining processes suitable for the material. Instead of the punctual loads of the previously common riveted joints, there is a surface-wide force transmission, which allows the same strengths with lower wall thicknesses and thus even further reduced structural weight respectively higher fuel savings. The pre-integration of the shells before closing the fuselage makes automated process management considerably easier compared to the status quo, so that both time requirements and costs can be reduced even further with a view to high-rate production.
... other branches
Together with the knowledge gained from the "MFFD" demonstrator, the Fraunhofer-Gesellschaft will make mature technology modules available for industrialization by interested companies. Other technologies will be incorporated into subsequent research projects in order to enable an even greater increase in efficiency with even lower resource consumption in future production. In addition to aircraft fuselages, target structures include vertical tail planes and tank systems for cryogenic hydrogen. Outside of the aviation industry, terrestrial or sea vehicles are also the focus of technology transfer.
Acknowledgments
The results described were developed by Fraunhofer in cooperation with the project partners (see https://s.fhg.de/9T4). Fraunhofer would like to thank the project partners for the successful cooperation and the European Commission for the funding.


Further information
Websites
Press release May 3, 2024: "New architecture for automated production of the world's largest thermoplastic aircraft fuselage demonstrated on a 1:1 scale"
Video and information l JEC Composites Awards 2025 Award Ceremony January 13, 2025
Trade Fair
JEC World 2025 l March 4 to 6, 2025 l Paris, France
- Fraunhofer IFAM l Hall 6, Booth Q24 l Joint booth Composites United e.V. https://s.fhg.de/QbCX
- Exhibitor area JEC Composites Awards 2025 l Hall 5 l Booth 5K157
Project partners involved in the "MFFD":
- Acroflight Ltd, Witham, UK
- Aernnova Aerospace S.A., Vitoria, Spain
- Aeromechs srl, Aversa, Italy
- AIMEN – Asociación de Investigación Metalúrgica del Noroeste, O Porriño, Spain
- Airbus
- Aitiip Centro Tecnológico, Zaragoza, Spain
- ALPEX Technologies GmbH, Mils, Austria
- BCC – Brunel Composites Centre, University London, UK
- CETMA – Centro di Ricerche Europeo di Technologie, Design e Materiali, Brindisi, Italy
- CT Engineering Group – Ct Ingenieros Aeronauticos de Automocion e Industriales Slu, Madrid, Spain
- CTI Systems, Lentzweiler, Luxembourg
- Diehl Aviation Laupheim GmbH, Laupheim, Germany
- Diehl Comfort Modules GmbH, Hamburg, Germany
- DLR – Deutsches Zentrum für Luft und Raumfahrt, ZLP Augsburg, Germany
- DLR – Deutsches Zentrum für Luft und Raumfahrt, ZLP Stade, Germany
- Element Materials Technology, Sevilla, Spain
- FADA – Andalusian Foundation for Aerospace Development / CATEC – Center for Advanced Aerospace Technologies, Sevilla, Spain
- FFT Produktionssysteme GmbH & Co. KG, Fulda, Germany
- Fraunhofer-Gesellschaft, Fraunhofer-Institut für Betriebsfestigkeit und Systemzuverlässigkeit LBF, Darmstadt, Germany
- Fraunhofer-Gesellschaft, Fraunhofer-Institut für Chemische Technologie ICT, Pfinztal, Germany
- Fraunhofer-Gesellschaft, Fraunhofer-Institut für Elektronische Nanosysteme ENAS, Chemnitz, Germany
- Fraunhofer-Gesellschaft, Fraunhofer-Institut für Fertigungstechnik und angewandte Materialforschung IFAM, Stade, Germany
- Fraunhofer-Gesellschaft, Fraunhofer-Institut für Gießerei-, Composite- und Verarbeitungstechnik IGCV, Augsburg, Germany
- Fraunhofer-Gesellschaft, Fraunhofer-Institut für Werkstoff- und Strahltechnik IWS, Dresden, Germany
- GKN Aerospace, Fokker Aerostructures BV, Papendrecht, Netherlands
- GKN Aerospace, Fokker ELMO BV, Hoogerheide, Netherlands
- HSLU – Hochschule Luzern, Luzern, Switzerland
- KVE Composites Group, The Hague, Netherlands
- LSBU – London South Bank University, London, UK
- NLR – Royal Netherlands Aerospace Centre, Marknesse, Netherlands
- Ostseestaal GmbH & Co KG, Stralsund, Germany
- Premium AEROTEC, Augsburg, Germany
- Rescoll, Pessac Cedex, France
- SAAB AB, Stockholm, Sweden
- SAM XL, Delft, Netherlands
- Techni-Modul Engineering, Coudes, France
- Technische Universität München, Lehrstuhl für Carbon Composites, München, Germany
- Technische Universiteit Delft, Delft, Netherlands
- TWI – The Welding Institute, Cambridge, UK
- UPAT – University of Patras, Patras, Greece
- XELIS GmbH, Herford, Germany
Photos
© Fraunhofer IFAM respectively © JEC Composites/SEB_DHALLOY, but can be published in reports about this press release.
www.ifam.fraunhofer.de/en/Press_Releases/Downloads.html
Photos and PDF for Download
Last modified: