Automated production technologies and new architectures for a 1:1 scale thermoplastic CFRP aircraft fuselage for sustainable aviation
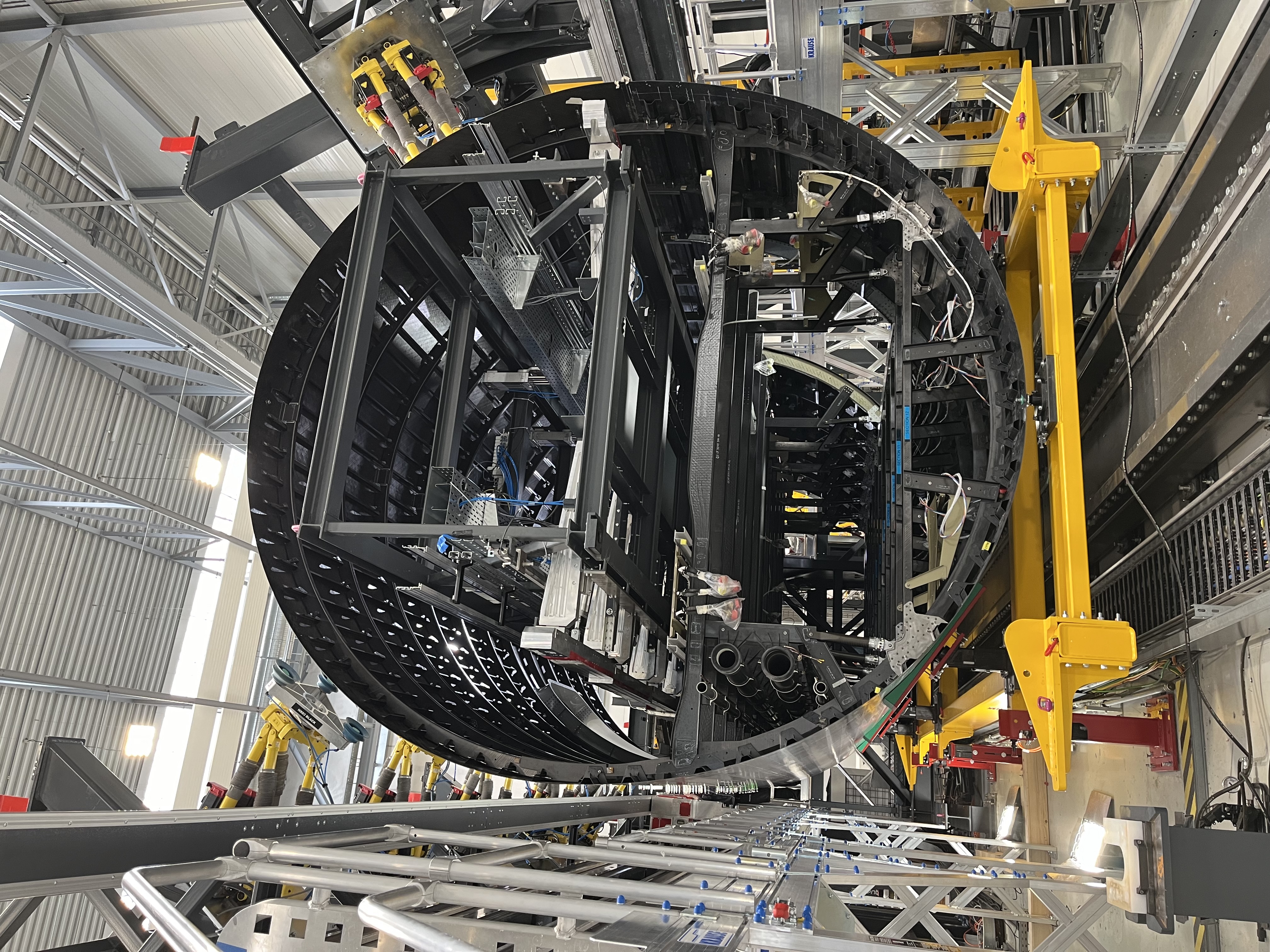
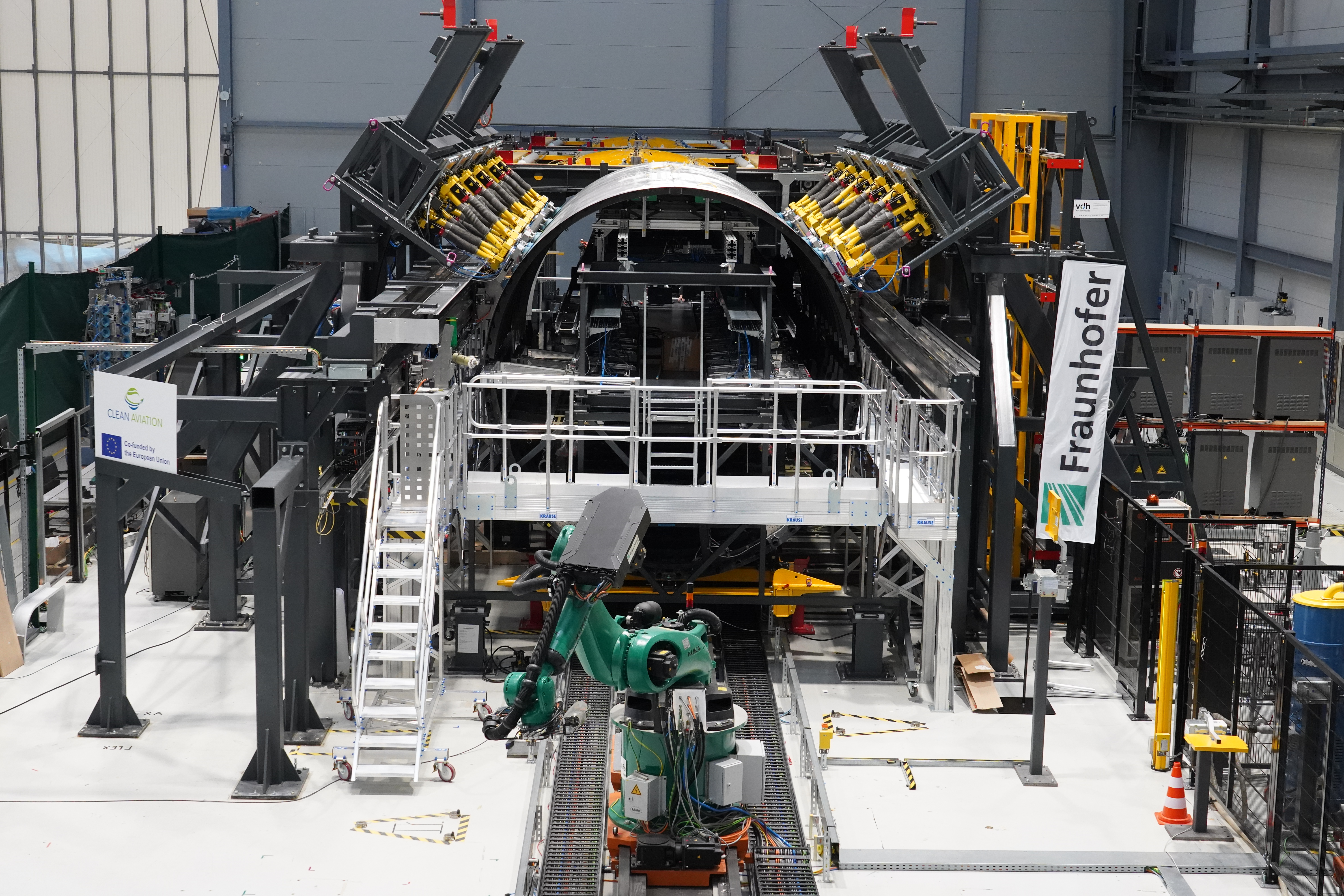
The European research program “CleanSky 2” addressed climate-friendly aviation with its activities. The aim was to sustainably reduce the emission of CO2, NOX and noise from flight operations. The joint project “CleanSky 2 – Large Passenger Aircraft” (“LPA”) focused on innovative, thermoplastic materials and architectures in order to reduce production times and thus costs in high-rate production as well as the weight of aircraft by around ten percent in each case. Considering the high quality and tolerance requirements typical of aviation, the production technologies also had to be re-thought to achieve the ambitious goals.
Within the CleanSky 2/Clean Aviation joint project “CleanSky 2 – Large Passenger Aircraft” (“LPA”), the Fraunhofer IFAM has been working on the automated production technologies and final assembly of the “Multi Functional Fuselage Demonstrator” (“MFFD”) in the “Major Component Assembly” (“MCA”) work package. In addition to the component size of the fuselage segment, which is eight meters long and four meters in diameter, the challenges were mainly due to the thermoplastic fiber composites used and the different welding connection techniques.
Automated production technologies enable high-rate capability in aircraft manufacturing
As part of the R&D work, the Fraunhofer-Gesellschaft in Stade, together with the joint partners, created the research platform “Multifunctional Automation System for Fuselage Assembly Line” (“MultiFAL”), which also integrates the research partners' technologies for the automated production of thermoplastic aircraft fuselages.
In contrast to easy implemented manufacturing organizations with individual technology stations, the integration of relevant process technologies into a multi-technology platform offers the advantage of being able to carry out production processes on one and the same component simultaneously, thus reducing cycle times and enabling higher production rates.
The eight-meter-long fuselage section of the MFFD has a total diameter of four meters and consists of two 180° shell elements. This component design presented a number of challenges, including the comprehensive transfer of the CAD-designed subsystems into a common model with uniform reference specifications, the accessibility of all joining points as well as potential collisions of the system's moving elements. Extensive simulations using CAD-supported investigations of space, stiffnesses and functional sequences provided a suitable tool for virtual pre-validation of the real structure.
High-precision alignment of the shell components using parallel kinematics
In the automated assembly of carbon fiber reinforced components (CFRP components), production-related component tolerances are one of the biggest challenges. The low dimensional accuracy of the components is a clear obstacle to the positioning accuracy of the joining partners required for the joining processes. The Fraunhofer IFAM in Stade is therefore researching technologies that can automatically correct the shape and position of large structural components – such as the two shell components of the MFFD – in the sub-millimeter range.
In the MultiFAL project, a total of ten hexapod robots were used to pick up the upper shell with vacuum suction grippers and align it with the lower shell in a collaborative movement. The advantage of using hexapods is that they can be aligned in all six degrees of freedom, which is particularly important for complex and unpredictable component deformations.
In addition to the orientation in the assembly space, the component geometry was also corrected according to the project’s target values. The robots were precisely controlled using closed-loop control with laser measurement data as input signals.
Providing structural components for automated manufacturing processes
Before the upper shell was aligned by hexapods, a specially designed, mobile component fixture positioned the lower shell in the assembly system. On the one hand, this component holder allowed the component to be clocked into the system and the finished fuselage structure to be clocked out; on the other hand, it also allowed the shape and orientation of the lower shell to be adjusted to the target geometry for assembly. In the subsequent process, the lower shell was considering static and only the upper shell was dynamically adjusted to reduce complexity.
As part of the joint project, the left longitudinal seam of the fuselage segment was joined using a continuous CO2 laser welding process. The part design provided for a stepped butt joint, in which up to six strips of the same thermoplastic material as the fuselage shell were placed on top of each other. With a material thickness of just 1 millimeter, the strips had a varying width of 6 to 36 centimeters and a length of up to 4.5 meters.
Automating the laser welding process also required automated feeding of these material strips. Due to their varying dimensions and low stiffness, the continuous insertion of the strips into the stepped structure of the joint following the welding process in the same operation created considerable handling challenges. Fraunhofer developed an end effector for this purpose, which was able to precisely position the strips on a linear axis along the longitudinal seam, reacting specifically to the different widths and lengths
The R&D work carried out by Fraunhofer IFAM at the Research Center CFK NORD in Stade as part of the LPA project is one of numerous research projects in which innovative solutions for the automated processing as well as assembly of large structures are being developed and technologies are being investigated, in particular under the boundary conditions of processes on a 1:1 scale.
Thanks to the funding of the joint project “CleanSky 2 – Large Passenger Aircraft” by the European Union and the excellent cooperation with national and international partners, it has been proven for the first time worldwide that the automation-compatible thermoplastic architecture for aircraft fuselages leads to both an increase in production efficiency for high-rate production and a significant reduction in weight. The ten percent weight reduction and ten percent production cost savings achieved in the project are far from exploiting the full potential of the combination of the new construction method with automated production.
The Fraunhofer IFAM in Stade offers solutions and expertise to tackle similar projects in the field of joining and assembly on a national and international level in the future. In a state-of-the-art and unique research environment, our partners and customers are provided with various technologies for automated surface pre-treatment, adhesive application, component handling and a range of measurement technologies as well as digital building blocks in the context of the smart factory for joint collaboration.