Reliable demolding, optimized efficiency and quality: release agent-free FRP large component production

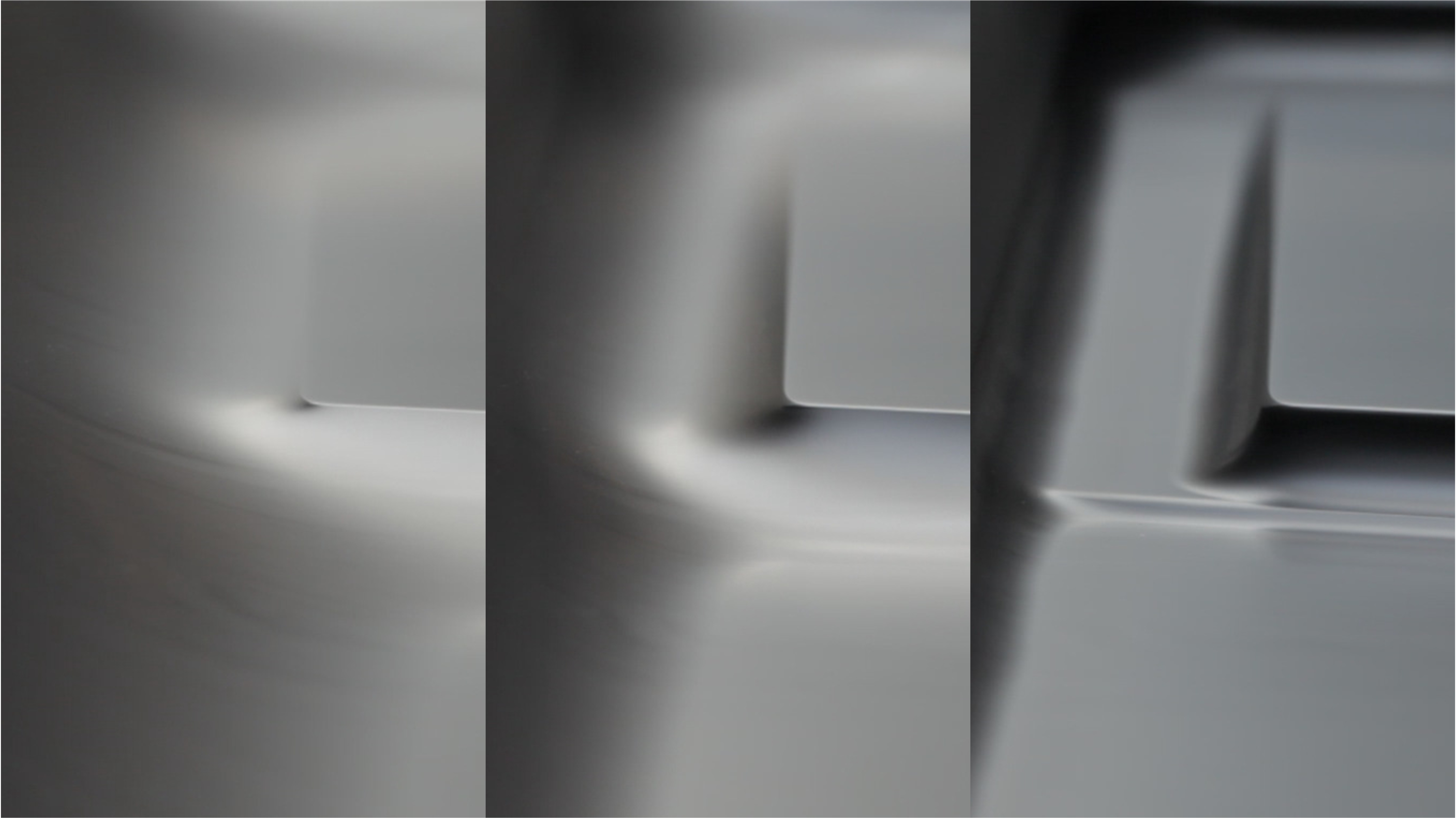
The PeelPLAS® release film - a advanced version of the FlexPLAS® release film - offers an alternative to conventional release agents in the production of components made from fiber-reinforced plastics (FRP). It enables reliable, release agent-free demolding of components ensuring clean mold and component surfaces without residue. Additionally it can protect components during mechanical processing and assembly, for example, and is compatible with common resin systems and in-mold coatings.
Time-, health- and labor-intensive: The challenge of release agent residues
Thanks to their low weight and high strength, FRP components are in particularly high demand in sectors such as the aviation, automotive and wind energy industries. Reliable demolding of the manufactured components is essential in order to meet the high demands on component and surface quality.
Until now, wet-chemical release agents have mostly been applied by wiping and spraying. These Health, Safety and Environment (HSE)-relevant substances require strict protective measures for employees. The removal of remaining release agent residues is time-consuming, as it prevents high-quality painting and adhesive bonding processes. This process is not only time-consuming and labor-intensive, but also requires additional health protection measures due to noise and dust emissions. The molds used must also be regularly cleaned of release agent residues in order to guarantee the required surface quality.
Residue-free, clean surfaces: PeelPLAS® release film for demanding applications - Especially for large structures
With the PeelPLAS® release film, Fraunhofer IFAM has developed a solution with which thermoset FRP components can be produced without the use of conventional release agent systems. The film is coated with an ultra-thin plasma-polymer release layer in a low-pressure plasma reactor, ensuring optimal adhesion to the polymer film and reliable release performance to most reactive resins. The highly elastic PeelPLAS® release film can withstand elongations of over 300 percent and is suitable for curing temperatures of up to 190 degrees Celsius. Applied to the mold with vacuum support, it conforms seamlessy to complex geometries - even on curved or structured molds.
Versatile application and advantages in large-scale productions
After component manufacture, the PeelPLAS® release film remains on the surface, providing protection against contamination during subsequent machining or assembly processes. The residue-free removal of the PeelPLAS® release film results in a clean component surface, which in many cases is immediately suitable for painting or adhesive bonding.
PeelPLAS® technology significantly reduces the amount of manual post-processing required, particularly in the production of large structures. The Stade branch offers ideal conditions for this: In the spacious R&D hall, machining, assembly and joining technologies are tested on components of various dimensions in original size with a high degree of automation.
Further development: PeelPLAS®-Paint for in-mold painting
PeelPLAS® technology is continuously evolving through close cooperation with industrial partners. One focus is the integration of in-mold painting using a pre-painted, plasma-polymer-coated release film. This pioneering solution is called PeelPLAS®-Paint and enables even more efficient surface finishing directly in the manufacturing process.
Semi-permanent composite film for multiple production cycles
A plasma-coated semi-permanent composite film is currently being developed as part of the 7th Energy Research Program. This innovation is intended to make the PeelPLAS® release film usable for several production cycles, which will further increase efficiency and sustainability. The NEOFOIL project builds on the findings of the successful OptiBlade project and continues to drive forward research in this area.
The PeelPLAS® release film technology opens up new and safer ways of producing FRP components without release agents. Thanks to the close cooperation between the Fraunhofer IFAM sites in Stade and Bremen, a smooth transfer of this technology to industrial application is guaranteed.
We accompany you from the first compatibility tests to the pilot series with competent support at both locations. In addition to test series in our laboratories and pilot plants, we also offer the opportunity to support you with the application of the release film on site.