Novel cooling system enables higher current density for electric motors
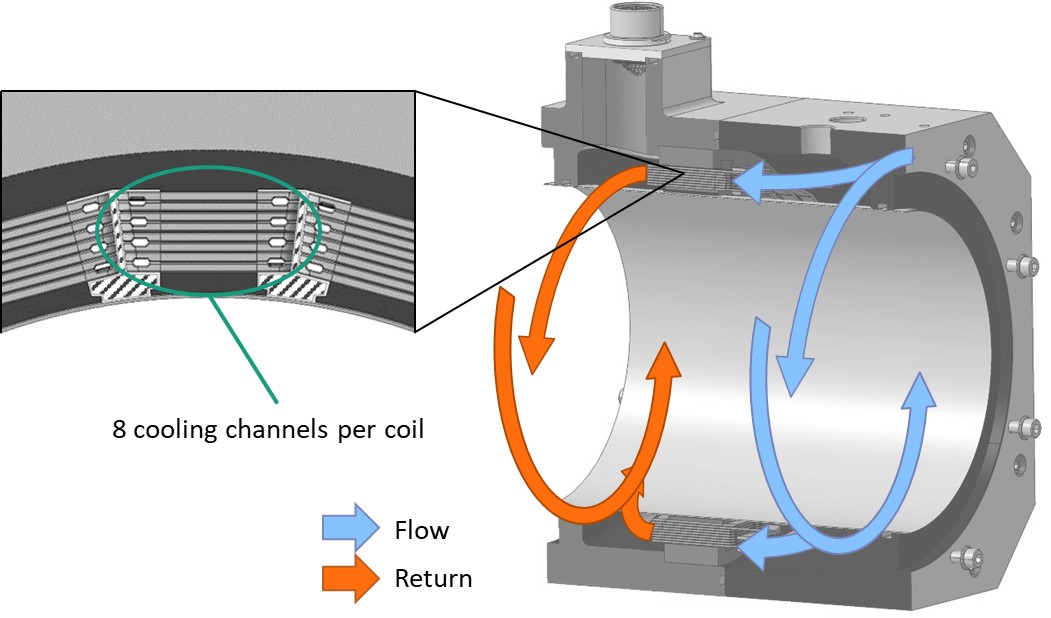
The ongoing electrification and the increasing use of inverter-powered electric motors present significant challenges for manufacturers and developers. Efficient integration of direct drives and the substitution of mechanical systems with electrical solutions demand innovative approaches. In particular, new solutions are required concerning the thermal endurance and performance of drive technology. To overcome the thermal limits in electric machines, a project developed an easily applicable direct fluid conductor cooling system for concentrated windings with integrated cooling channels. Extensive testing on our test bench successfully demonstrated the potential of this technology to increase torque and current density in electric drives. We managed to increase the current density to up to 51.25 A/mm² while simultaneously achieving torques of up to 248.5 Nm. This represents a significant advancement compared to conventional cooling methods.
Extreme increase in torque density through direct conductor cooling
With the increasing electrification of mobility, interest in ever more powerful electric motors is growing. In many machines and systems, inverter-powered electric motors are being used more frequently. There is a trend toward replacing traditional mechanical drives, such as hydraulic drives, with electric drives. However, hydraulic drives are still indispensable in certain areas due to their very high torque outputs.
The thermal limits of electric machines, primarily determined by the permissible temperature of the insulation system, are a limiting factor in increasing their torque or current density. Therefore, the focus of the R&D project was on the goal of significantly increasing torque density through alternative cooling technologies. While electric machines typically use air or water jacket cooling, this project pursued the use of direct fluid conductor cooling for concentrated windings with integrated cooling channels. To realize such cooling, Fraunhofer IFAM employed casting technologies for manufacturing the electric coils.
Prototype of a permanent magnet synchronous machine (PMSM) with embedded cooling system
As part of the project, an electric machine based on a "High-Torque" motor was designed, calculated, mechanically constructed and assembled. Systematic variations to the geometric and electrical parameters of the base machine led to extensive insights into the design of PMSMs with high current density and direct conductor cooling. These insights were incorporated into the resulting design rules and guidelines for the dimensioning of such machines.
The results of the presented project demonstrate that the substitution of hydraulic motors is possible, thus opening new applications for electric machines. Moreover, they provide manufacturers and users in electric drive technology with precise information on the dimensioning, calculation, and real operating behavior of synchronous machines at very high current densities. This is of great significance for the accurate dimensioning and calculation of electric machines with direct fluid conductor cooling system, leading to a reduction in development time and costs. We make this information available to manufacturers and developers to support them in making informed decisions for the design of their drives and the transitioning to mass production.
Your partner for the development of innovative electric drives
Fraunhofer IFAM offers comprehensive expertise in the development of electric drives. These drives can be used in mobile applications such as aircraft and vehicles, as well as in stationary industrial applications. With an interdisciplinary team, we possess the necessary competencies in manufacturing technology and applied materials research, as well as in the design and development of electric machines, to provide our clients with solid decision-making bases, digital models, and targeted consultation. Our goal is to assist companies in transferring manufacturing innovations from science to industrial applications.