Optimized dynamics and stability through the combination of gear and direct drive

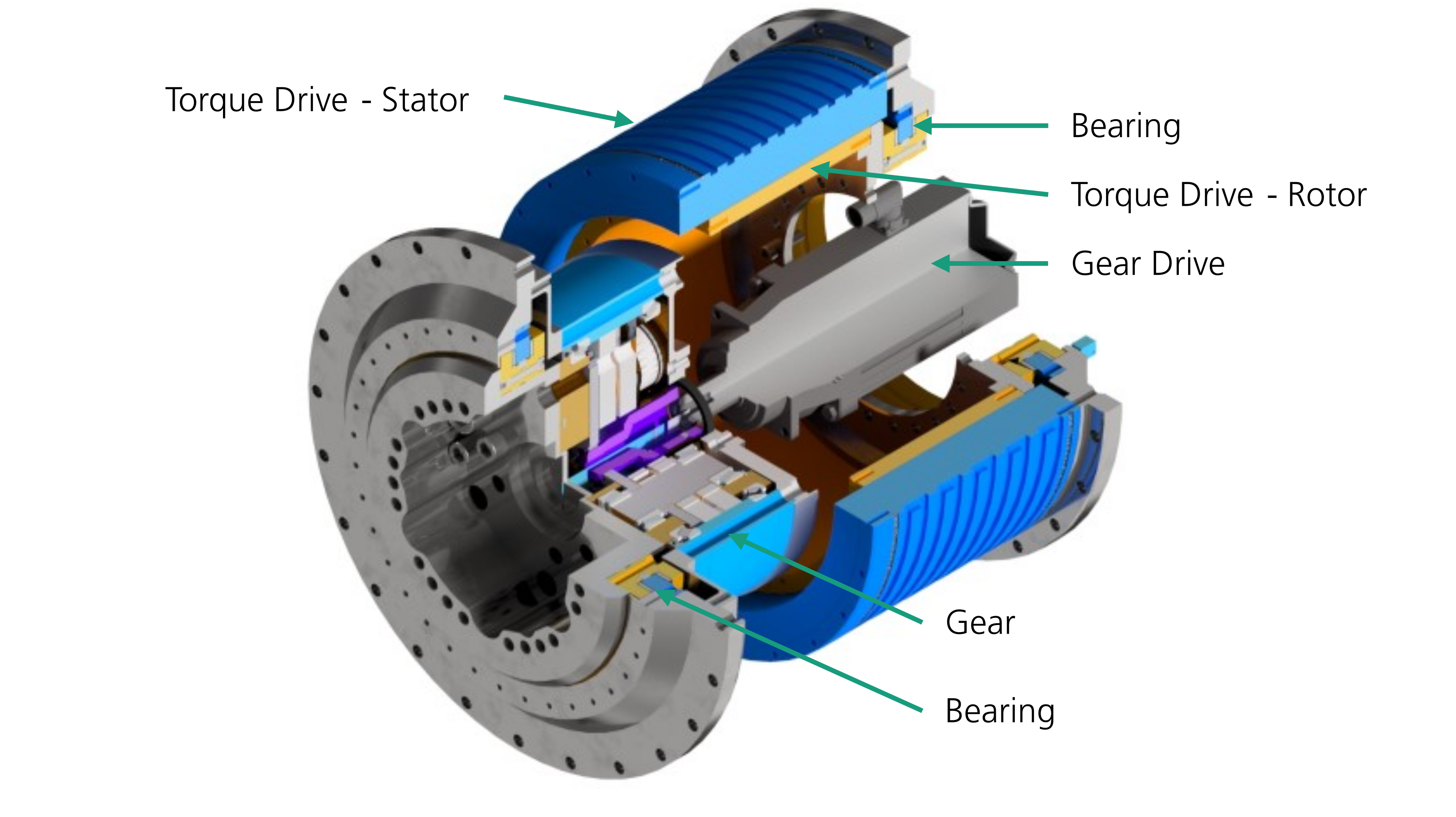

Industrial robots have become an integral part of modern production processes. Their serial kinematic design ensures a high degree of flexibility while taking up little mounting space. Fraunhofer IFAM in Stade, Germany has now developed a novel solution for the dynamic improvement of these kinematics: the hybrid drive for industrial robots.
The hybrid drive combines the proven gear drive with an additional direct drive, allowing a torque to be applied directly on the load side. This combination enables targeted compensation of undesirable gearbox effects and effective damping of high-frequency excitations - with maximum energy efficiency. Both drives run in parallel and follow the identical position value. The direct drive controls the dynamic part, while the gear drive takes over the static and quasi-static loads.
This innovative drive control system ensures high energy efficiency and maximum precision: The direct drive is only actively powered during the acceleration and braking phases, which minimizes energy consumption. At the same time, the damping within the drivetrain is increased so that the resonance frequencies no longer result from the base axes, but from the structure and bearings of the system. This significantly reduces the transmission of vibrations, resulting in more stable and precise control of the drive and therefore the entire kinematics.
This optimized drive technology not only improves the dynamics and responsiveness of the system, but also its resistance to external disturbances such as process forces. Industrial robots with hybrid drives therefore achieve higher performance and precision - decisive factors for applications that require maximum path accuracy and stability.
Improved path accuracy and constant behavior in the workspace
The improved path accuracy of the robot through the drive system represents a major improvement. Path accuracy tests carried out using the ISO 9283 test track show a significant increase in path accuracy to less than 0.1 mm. This test track includes various geometric elements such as corners, circles and changes of direction, which are crucial for evaluating the performance of the system.
A key feature of this system is the avoidance of path errors at sharp geometric elements such as corners. The path error is also significantly reduced at reversal points and changes of direction.