Optimierte Dynamik und Stabilität durch die Kombination von Getriebeantrieb und Direktantrieb

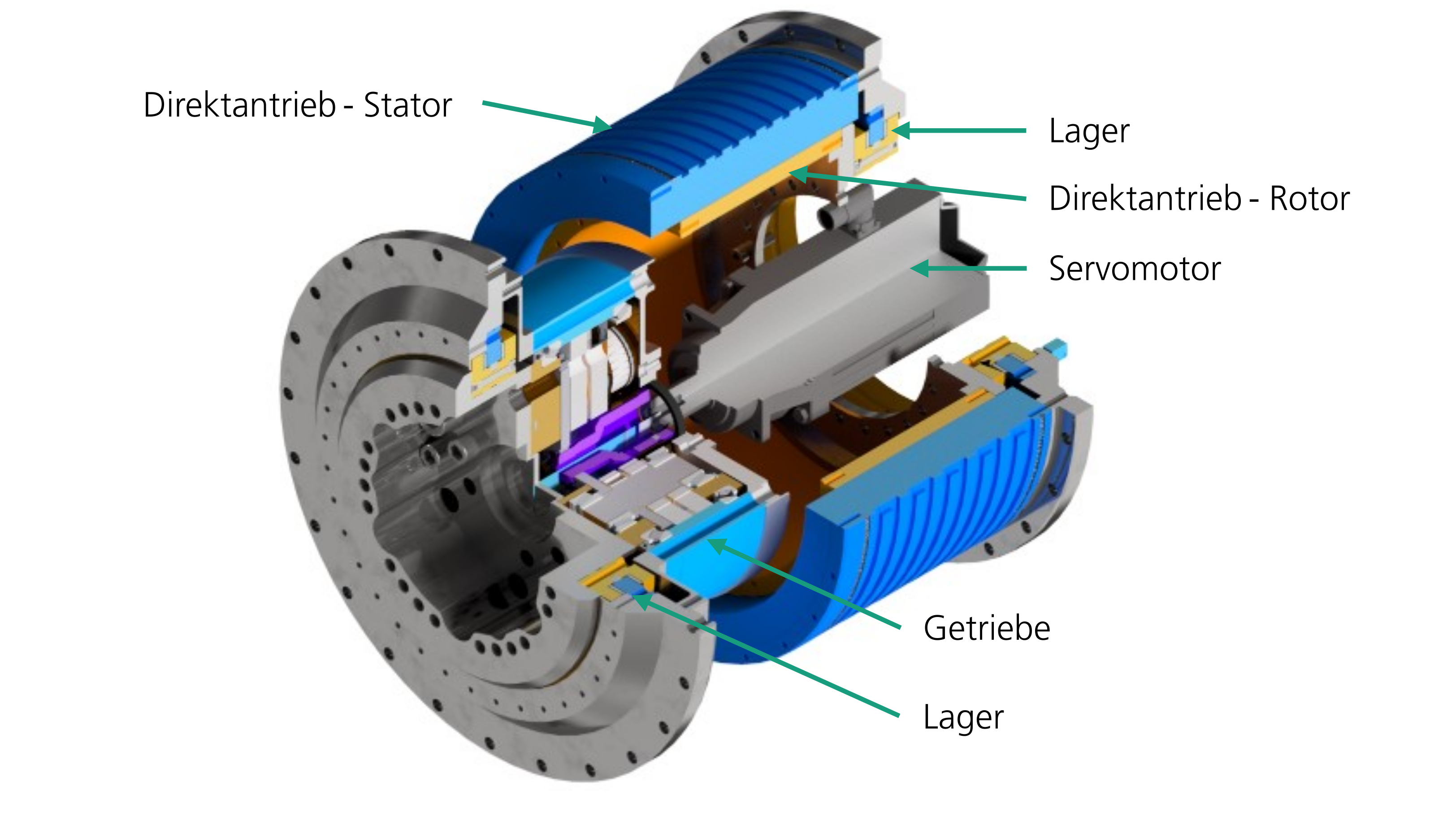

Industrieroboter sind aus modernen Produktionsprozessen nicht mehr wegzudenken. Ihr serieller kinematischer Aufbau sorgt für hohe Flexibilität bei gleichzeitig geringem Platzbedarf. Das Fraunhofer IFAM in Stade hat nun eine neuartige Lösung zur dynamischen Verbesserung dieser Kinematik entwickelt: den Hybridantrieb für Industrieroboter.
Der Hybridantrieb kombiniert den bewährten Getriebeantrieb mit einem zusätzlichen Direktantrieb, wodurch direkt auf der Lastseite ein Moment aufgeschaltet werden kann. Diese Kombination ermöglicht die gezielte Kompensation unerwünschter Getriebeeffekte sowie die effektive Dämpfung von Anregungen hoher Frequenzen – und das bei maximaler Energieeffizienz. Beide Antriebe laufen parallel und folgen dem identischen Positionswert. Dabei regelt der Direktantrieb den dynamische Anteil, während der Getriebeantrieb die statischen und quasistatischen Lasten übernimmt.
Diese neuartige Antriebssteuerung sorgt für eine hohe Energieeffizienz und höchste Genauigkeiten: Der Direktantrieb wird nur während der Beschleunigungs- und Bremsphasen aktiv bestromt, was den Energieverbrauch minimiert. Gleichzeitig erhöht sich die Dämpfung innerhalb des Antriebsstrangs, sodass die Resonanzfrequenzen nicht mehr aus den Basisachsen resultieren, sondern aus der Struktur und den Lagern des Systems. Dadurch wird die Übertragung von Schwingungen erheblich reduziert, was zu einer stabileren und präziseren Steuerung des Antriebs und damit der gesamten Kinematik führt.
Durch diese optimierte Antriebstechnologie verbessert sich nicht nur die Dynamik und Reaktionsfähigkeit des Systems, sondern auch die Widerstandsfähigkeit gegen externe Störungen, wie Prozesskräfte. Industrieroboter mit Hybridantrieben erreichen somit eine höhere Leistung und Präzision – entscheidende Faktoren für Anwendungen, die höchste Bahngenauigkeit und Stabilität erfordern.
Verbesserte Bahngenauigkeit und konstantes Verhalten im Arbeitsraum
Die verbesserte Bahngenauigkeit des Roboters durch das Antriebssystem stellen einen entscheidenden Fortschritt dar. Untersuchungen zur Bahngenauigkeit, die anhand der ISO 9283 Prüfbahn durchgeführt wurden, zeigen eine signifikante Steigerung der Bahngenauigkeit auf unter 0,1 mm. Diese Prüfbahn umfasst verschiedene geometrische Elemente wie Ecken, Kreise