Efficient assembly of large structures: New approaches through automation and digitalization in joining processes
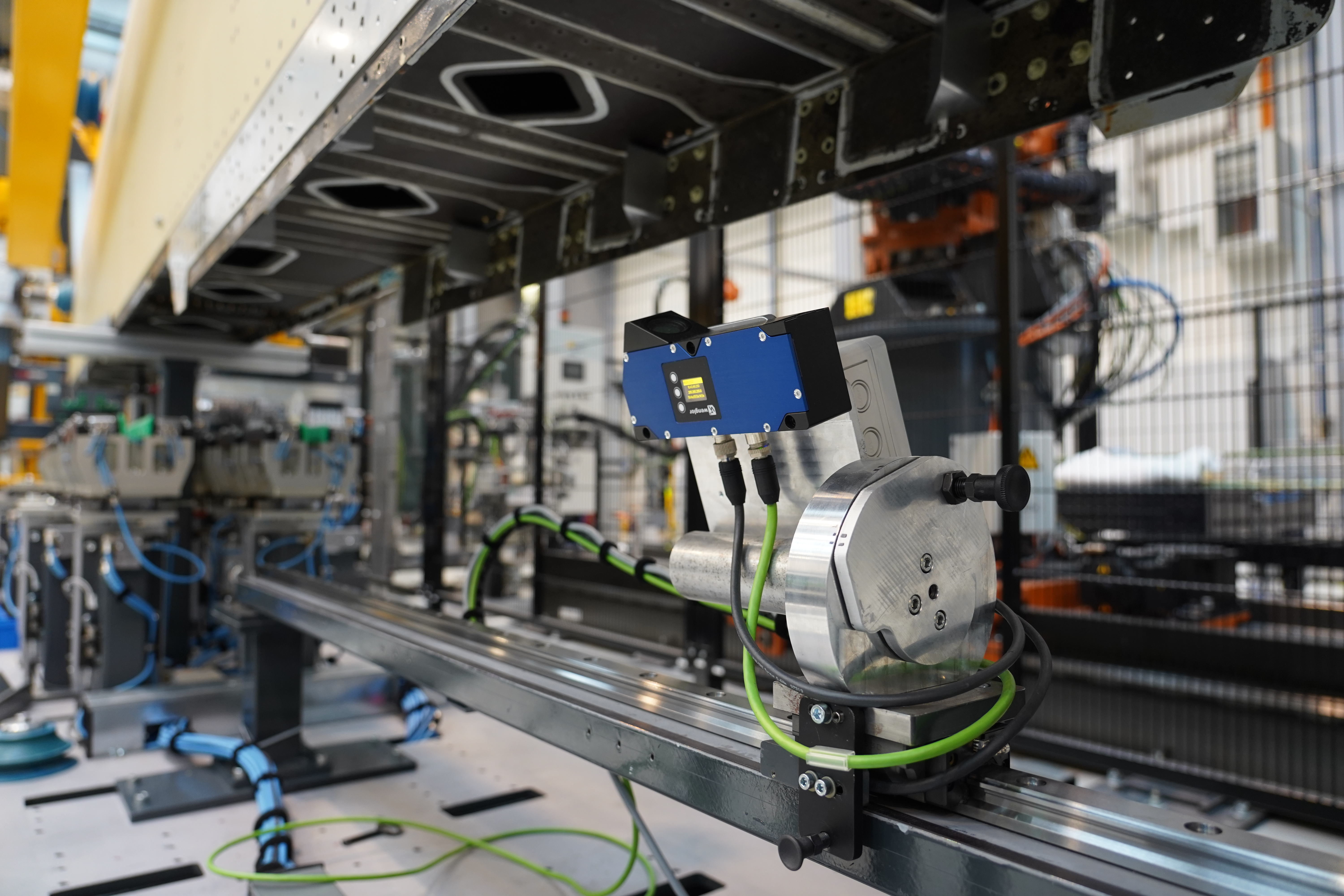

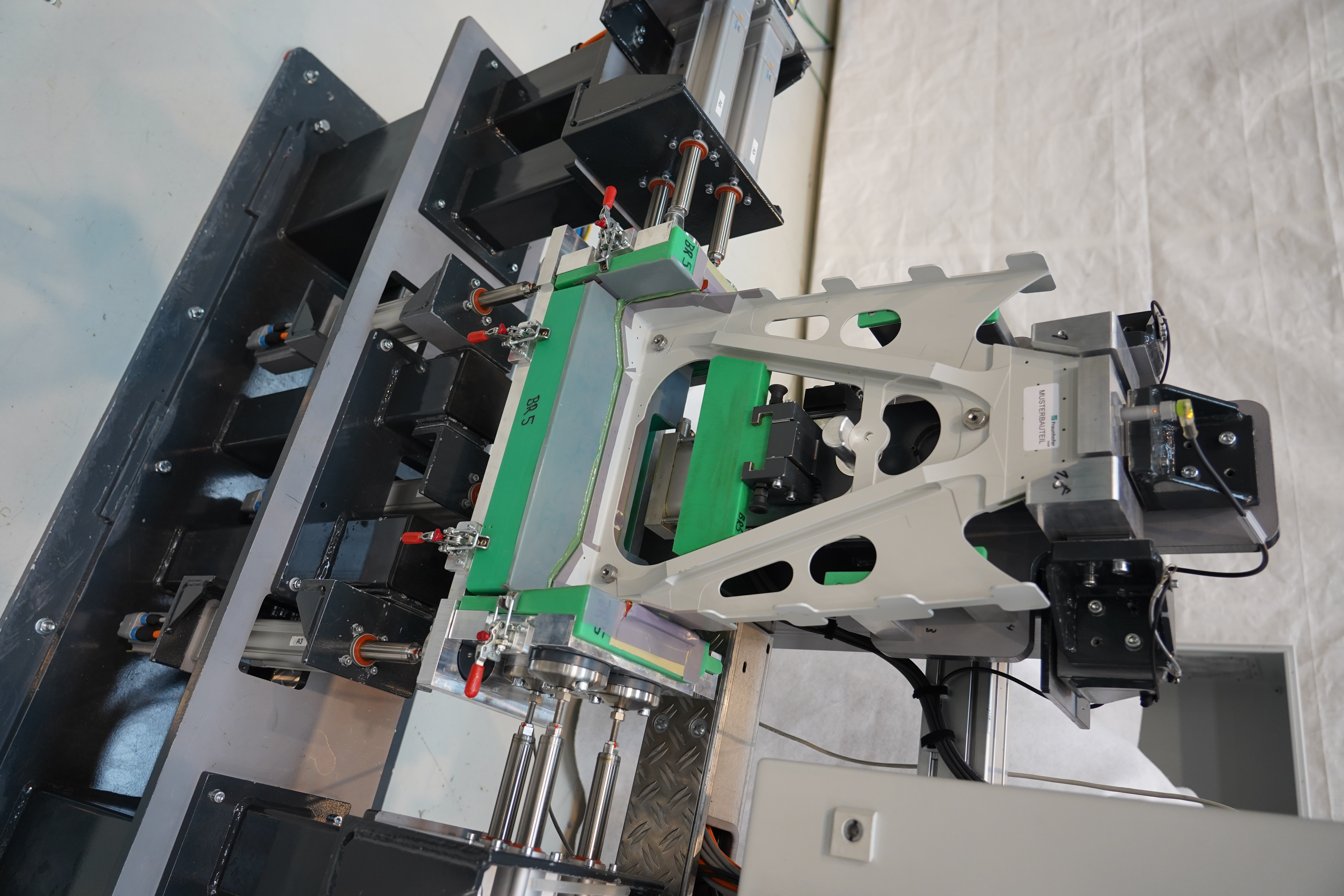
As part of the “Fast-FlexMont2” research project, the Fraunhofer Institute for Manufacturing Technology and Advanced Materials IFAM in Stade, Germany, has demonstrated an automation solution for the efficient assembly of large structures on a 1:1 scale. The use of advanced measuring and referencing methods, high-precision positioning technologies as well as the implementation of continuous digital process control resulted in a decoupled process for automated tolerance compensation of aircraft components. Downtimes was reduced and the efficiency of the joining processes in the vertical tail plane assembly – the focus of the project – was increased.
The application extends beyond aviation and comparable efficiency benefits can also be achieved in other industries by making minor adjustments to the solutions.
Aim of the “Fast-FlexMont2” project (“Research on agile production technologies for CFRP box structures”), funded by the German Federal Ministry of Economic Affairs and Climate Action (BMWK), was the development of a solution to increase efficiency in the assembly of aircraft vertical tail planes. The high-precision positioning of components, particularly in aircraft construction, plays a key role here. In collaboration with Airbus and FFT Produktionssysteme, a method was developed in which a special pasty shim material was automatically applied onto a rudder hinge outside the assembly line and cured before installation in the vertical tail plane. The gap-filling material was used to compensate any inaccuracies arising during the assembly of components on structures with tight tolerances.
Digitalization as an enabler for the parallelization of processes
The parallelization of work steps within the production process was made possible in particular by the sensor-based detection of the surface geometry of the respective joining areas. In the assembly process, which was initially carried out virtually, the precise gap volumes for the shim application were calculated by combining measurement data and target positions. This adaptive process could then be performed at a remote station independently of the vertical tail plane, eliminating downtimes and waiting times. Automated and digitally networked processes made it possible to respond to part tolerances on the one hand and to the variance of the differently dimensioned rudder hinges on the other. Volumetric metering and application as needed as well as the precise shaping and edge smoothing of the shim based on a digital best-fit determination and the values calculated from it. After the gap filling cured, the finished shimmed rudder hinge was inserted into the vertical tail plane.
Process automation using lightweight robotics
Lightweight, robotic assembly aids were used for component handling and precise positioning, facilitating manual production processes while ensuring consistent quality. In addition to agile production, this optimization reduces the downtime of technical resources by parallelizing operations, which also increased productivity and reduced costs.
Potential for reducing costs and increasing efficiency also for other sectors
The idea of automatically applying and curing gap-filling material to compensate for geometric tolerances during assembly is not limited to aircraft vertical tail planes. The adaptability of the system allows it to be applied to other structures as well as other industries, such as the production of rail vehicles, ships, commercial vehicles and wind power plants. The advantages are obvious: cost savings and increased efficiency are not only important for the aerospace industry, but are also worth pursuing in other sectors.