Effiziente Montage von Großstrukturen: Neue Wege durch Automatisierung und Digitalisierung in Fügeprozessen
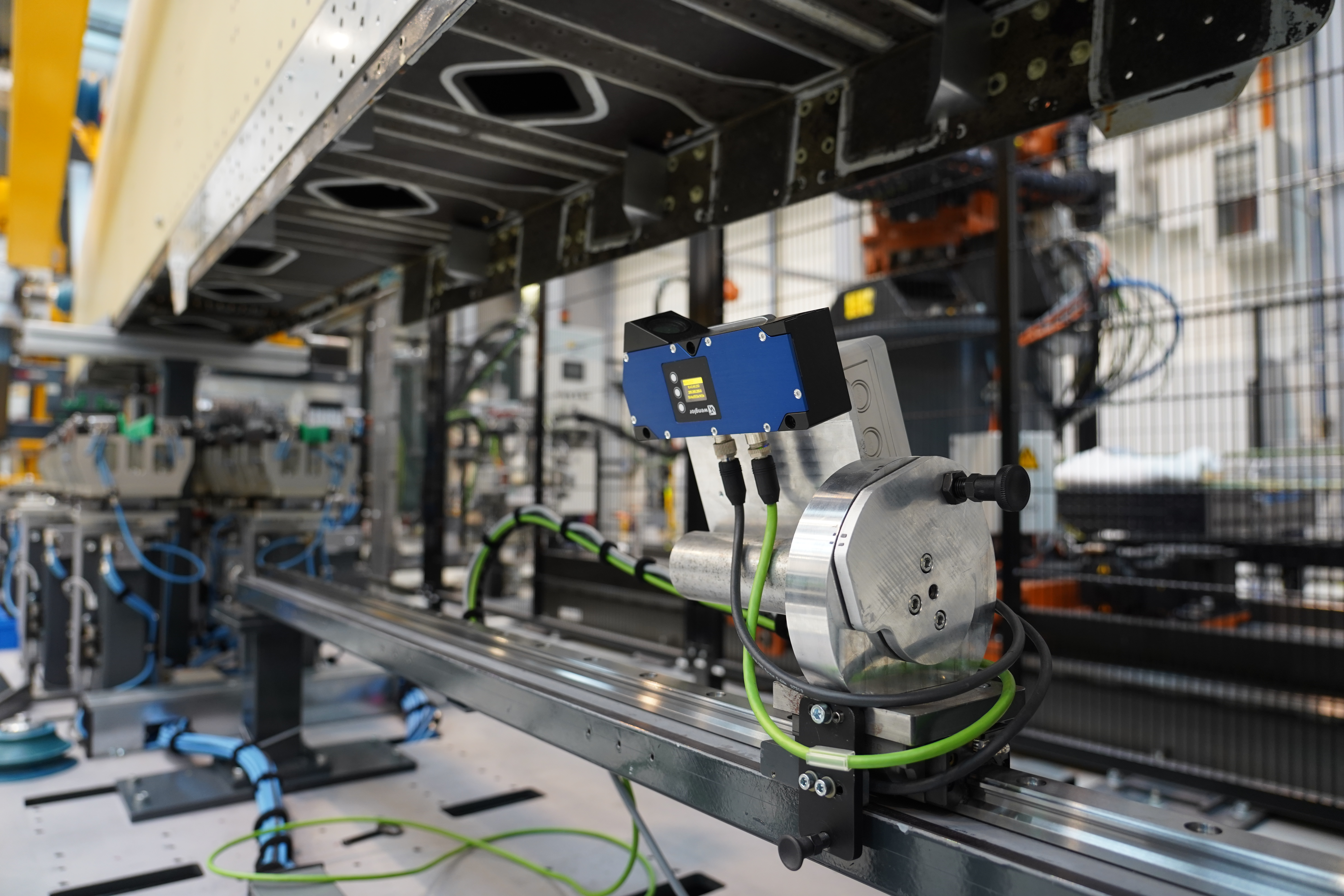
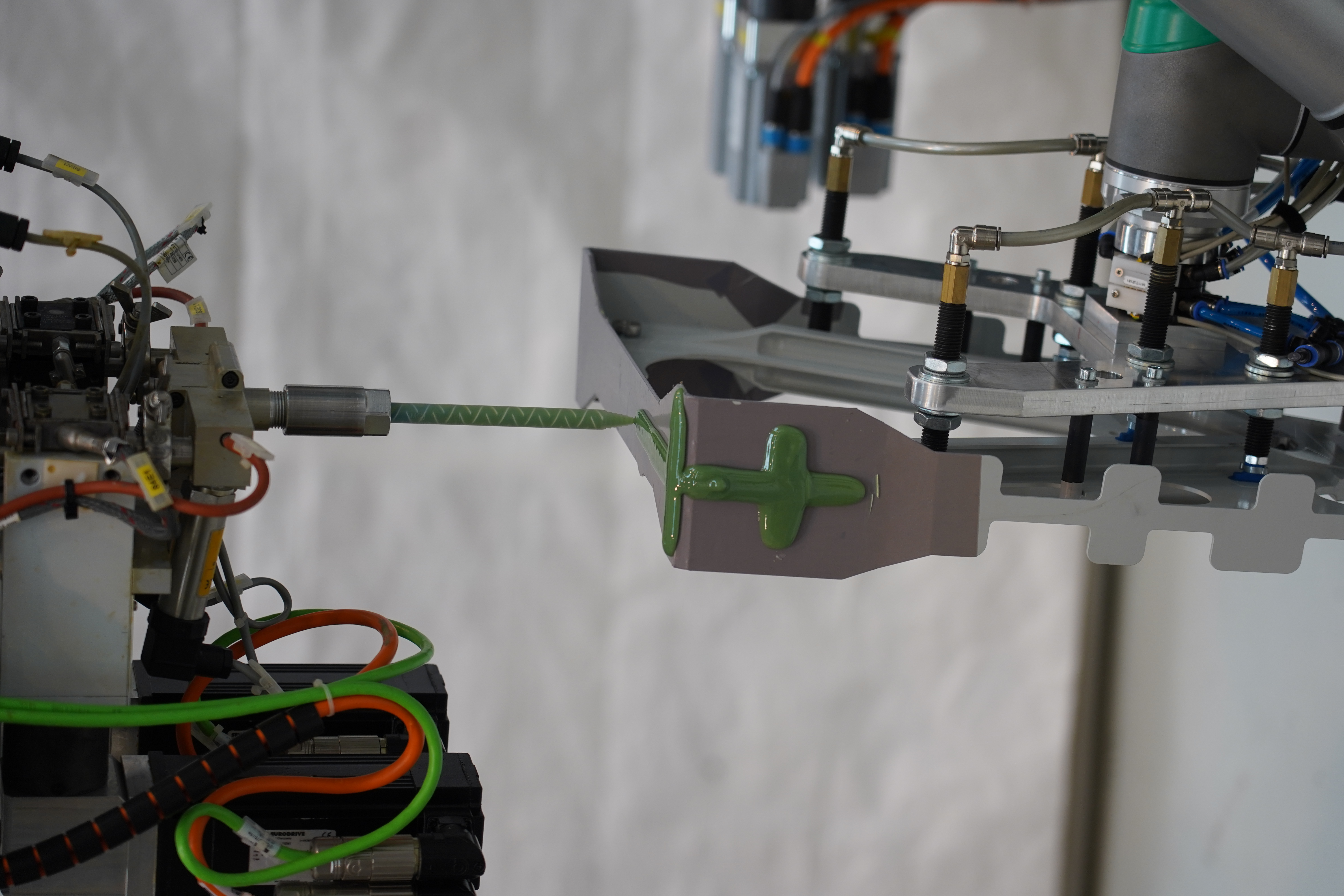

Das Fraunhofer-Institut für Fertigungstechnik und Angewandte Materialforschung IFAM in Stade hat im Rahmen des Forschungsprojekts »Fast-FlexMont2« eine Automatisierungslösung zur effizienten Großstrukturmontage im 1:1-Maßstab demonstriert. Durch den Einsatz fortschrittlicher Mess- und Referenzierungsmethoden, hochpräziser Positionierungstechnologien sowie die Implementierung einer kontinuierlichen digitalen Prozesssteuerung resultierte ein entkoppelter Prozess zum automatisierten Toleranzausgleich von Flugzeugbauteilen. Standzeiten konnten reduziert und die Effizienz der Fügeprozesse in der im Projekt fokussierten Seitenleitwerksmontage erhöht werden.
Die Anwendung reicht über die Luftfahrt hinaus und vergleichbare Effizienzgewinne lassen sich durch kleinere Anpassungen der Lösungen auch in anderen Industriezweigen erzielen.
Im Rahmen des Projekts »Fast-FlexMont2« (»Forschung zu agilen Produktionstechnologien für CFRP-Boxstrukturen«), gefördert vom deutschen Bundesministerium für Wirtschaft und Klimaschutz (BMWK), wurde eine Lösung entwickelt, um die Effizienz bei der Montage von Flugzeugseitenleitwerken zu erhöhen. Dabei spielt die hochpräzise Positionierung von Bauteilen, insbesondere im Flugzeugbau, eine entscheidende Rolle. In Zusammenarbeit mit Airbus und FFT Produktionssysteme GmbH & Co. KG entstand eine Methode, bei der ein spezielles, pastöses Shim-Material abseits der Montagelinie automatisiert auf eine Rudergabel aufgetragen und vor Einbau in das Seitenleitwerk ausgehärtet wurde. Das eingesetzte spaltfüllende Material diente dem Ausgleich entstehender Ungenauigkeiten bei der Montage von Bauteilen an toleranzbehafteten Strukturen.
Digitalisierung als Enabler zur Parallelisierung von Prozessen
Ermöglicht wurde die Parallelisierung von Arbeitsschritten innerhalb der Produktion insbesondere durch die sensorische Erfassung der Oberflächengeometrie der jeweiligen Fügebereiche. In der zunächst virtuell durchgeführten Montage erfolgte die für die Shim-Applikation maßgebende Berechnung der genauen Spaltvolumen durch Zusammenführen von Messdaten und Sollpositionen. Dieser adaptive Prozess konnte danach unabhängig vom Seitenleitwerk an einer ausgelagerten Station erfolgen, wodurch sich Stillstand- und Wartezeiten vermeiden ließen. Dabei erlaubten automatisierte und digital vernetzte Prozesse einerseits auf die Bauteiltoleranzen und anderseits auf die Varianz der unterschiedlich dimensionierten Rudergabeln zu reagieren. Das volumengenaue Dosieren und bedarfsgerechte Auftragen sowie die präzise Formgebung und Kantenglättung des Shims basierte auf einer digital durchgeführten Best-Fit-Ermittlung und den daraus berechneten Werten. Nach Aushärtung der Spaltfüllung wurde die fertig geshimmte Rudergabel in das Seitenleitwerk eingesetzt.
Prozessautomatisierung mittels Leichtbaurobotik
Für das Bauteilhandling und das präzise Positionieren kamen leichte, roboterbasierte Montagehilfesysteme zum Einsatz, die manuelle Fertigungsprozesse erleichterten und gleichzeitig eine konsistente Qualität sicherstellten. Neben der agilen Fertigung ermöglichte diese Optimierung auch die Reduzierung von Standzeiten technischer Ressourcen durch die Parallelisierung von Arbeitsschritten, was zudem die Produktivität steigerte und die Kosten senkte.
Potenzial der Kostenreduktion und Effizienzsteigerung auch für andere Branchen
Die Idee, spaltfüllendes Material zum Ausgleich geometrischer Toleranzen in der Montage automatisiert aufzutragen und auszuhärten, ist nicht nur auf Flugzeugseitenleitwerke beschränkt. Durch die Anpassungsfähigkeit des Systems kann es sowohl für andere Strukturen als auch in anderen Branchen – wie Schienenfahrzeug-, Schiffs-, Nutzfahrzeug- und Windenergieanlagenbau – eingesetzt werden. Die Vorteile liegen auf der Hand: Kosteneinsparungen und Effizienzsteigerung sind nicht nur für die Luftfahrtindustrie von Bedeutung, sondern auch in anderen Sektoren erstrebenswert.