Aluminium statt Kupfer: Gegossene Aluminiumspulen senken Rohstoffkosten und Gewicht in industriellen elektrischen Maschinen
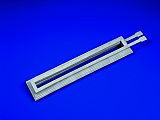
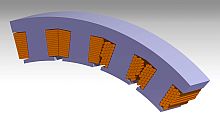
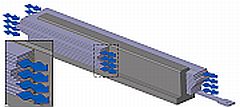
In Zusammenarbeit mit der Lloyd Dynamowerke GmbH & Co. KG in Bremen hat das Fraunhofer-Institut für Fertigungstechnik und Angewandte Materialforschung IFAM erstmals eine Aluminiumwicklung im Lost Foam-Gießverfahren für Großmotoren entwickelt. Die Aluminiumspule wurde für einen Kranmotor hergestellt, anschließend verbaut und jetzt erfolgreich getestet. Ergebnis: Ein technisch besserer Ersatz für die ursprünglich eingesetzten Kupferspulen ist gelungen. Der Füllfaktor und die Kühlleistung konnten durch die Gestaltungsfreiheit in der Gießtechnik deutlich gesteigert werden. Der Einsatz von Aluminiumspulen ermöglicht darüber hinaus eine Senkung der Rohstoffkosten und des Gewichts sowie eine Verringerung der Verluste.
Die Anforderungen an die Wicklungen elektrischer Maschinen sind vielfältig. Neben einem hohen Füllfaktor zur Minimierung des Leiterwiderstands müssen auch eine ausreichende Kühlung und die Reduzierung frequenzabhängiger Zusatzverluste gewährleistet sein. Gleichzeitig sollte der Herstellungsprozess so flexibel und kostengünstig wie möglich sein. Am Fraunhofer IFAM wurde daher ein Verfahren zur gießtechnischen Herstellung von Spulen entwickelt, mit dem bedeutende Vorteile gegenüber allen bekannten Wickeltechniken erzielt werden. Bei konventionell gewickelten Spulen wird im Durchschnitt ein Nutfüllfaktor von etwa 50 Prozent erreicht. Die weitgehend frei gestaltbare Leitergeometrie in der Gießtechnik ermöglicht die Realisierung von Füllfaktoren über 90 Prozent.
Fertigungstechnische Umsetzung – Gießen statt Wickeln
Als Gießverfahren wird das Feingussverfahren oder das Lost Foam-Verfahren eingesetzt. Um die Einbringung des Formmaterials bzw. des Formstoffes zu ermöglichen, wird die dargestellte Leitergeometrie gestreckt und mit einem Angusssystem versehen. Die Streckung der Spule ermöglicht auch das anschließende Aufbringen einer Isolationsbeschichtung, wobei abhängig von den Anforderungen in Bezug auf Spannungsfestigkeit, Schichtdicke und Temperaturbeständigkeit verschiedene Verfahren eingesetzt werden können. Leiterquerschnitte von ca. 4 mm² bis hin zu mehreren 100 mm² lassen sich damit realisieren. Die in der konventionellen Wickeltechnik zwangsläufig einzuhaltenden Biegeradien entfallen dabei vollständig.
Aluminium versus Kupfer
Durch die Verwendung des Aluminiums konnten die Rohstoffkosten gegenüber Kupferspulen von etwa 52.- Euro um über 85 Prozent auf 6.- Euro pro Spule gesenkt werden. Trotz der geringeren spezifischen elektrischen Leitfähigkeiten ist der elektrische Widerstand der Aluminiumspule infolge des erhöhten Nutfüllfaktors nicht höher als bei der Kupferspule. Die gefertigten Wendepolspulen der 330 kW Gleichstrommaschine sind unter Berücksichtigung der Möglichkeiten des Verfahrens geometrisch so gestaltet worden, dass neben der Maximierung der Leiterfläche auch die Entwärmung gegenüber den zuvor eingesetzten gewickelten Kupferspulen verbessert wird. In einem Prüfstandsversuch wurden die Temperaturen der Aluminium-Wendepolspulen im Dauerbetrieb mit den Temperaturen der Ausgangs-Kupferspulen verglichen. Durch die verbesserte Kühlung verringert sich der Temperaturhub der Wendepole im Dauerlauf von 75 auf etwa 45 Kelvin. Das geringere Temperaturniveau führt hierbei auch zu einer leichten Reduzierung der Gesamtverluste in der Maschine.
Die gießtechnische Herstellung ermöglicht es, die Kupferspule durch eine elektrisch äquivalente Aluminiumwicklung zu ersetzen und dabei Rohstoffkosten, Gewicht und Verluste einzusparen. »Die durch die Gießtechnik erzielte Verbesserung der Kühlleistung hat unsere Erwartungen übertroffen«, so der Entwicklungsingenieur Michael Jakob von den Lloyd Dynamowerken. »Wir sehen in dieser Technologie mit ihren gestalterischen Freiheiten auch das Potenzial, in zukünftigen Anwendungen Wirkungsgrad und Leistungsdichte elektrischer Maschinen zu steigern« ergänzt Jakob.
Letzte Änderung: