Gap-Filling - Vermeidung von Feuchtigkeits- und Gaseinschlüssen bei thermoplastischen Faserverbund-Großstrukturen durch automatisiertes Spaltfüllen
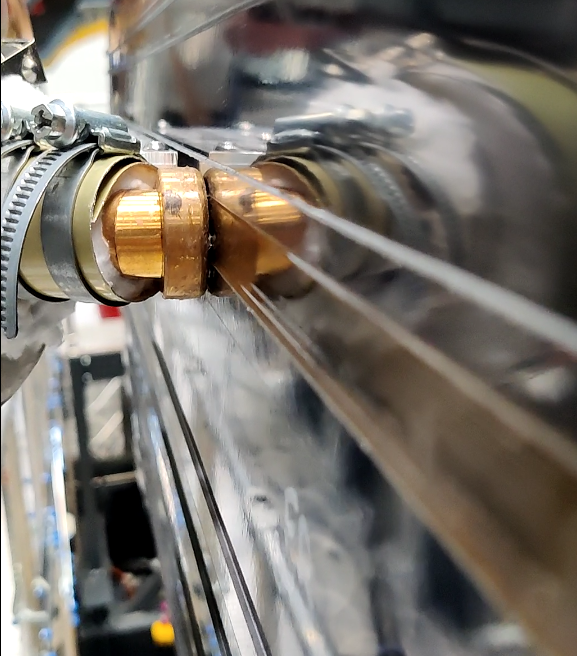
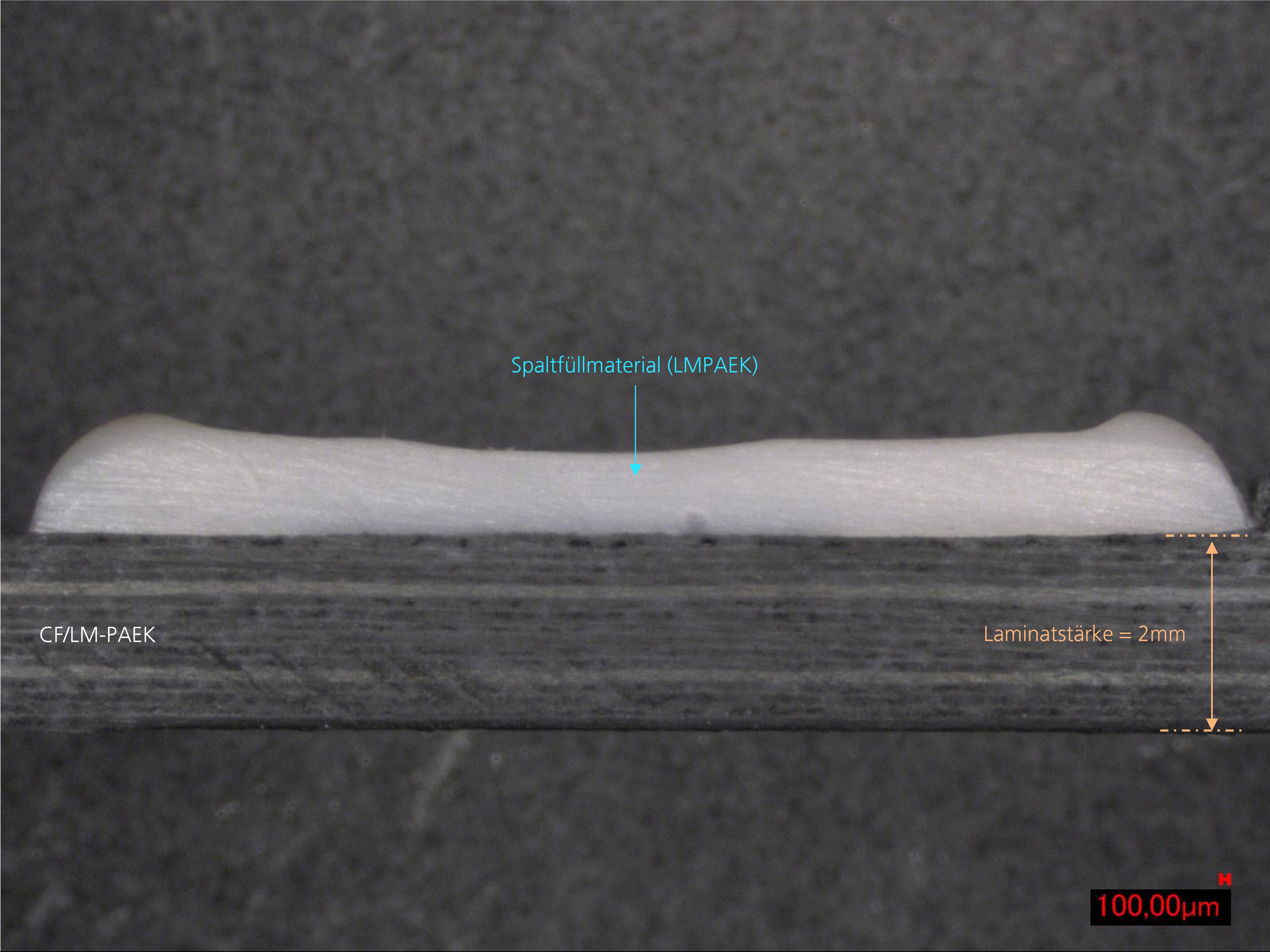
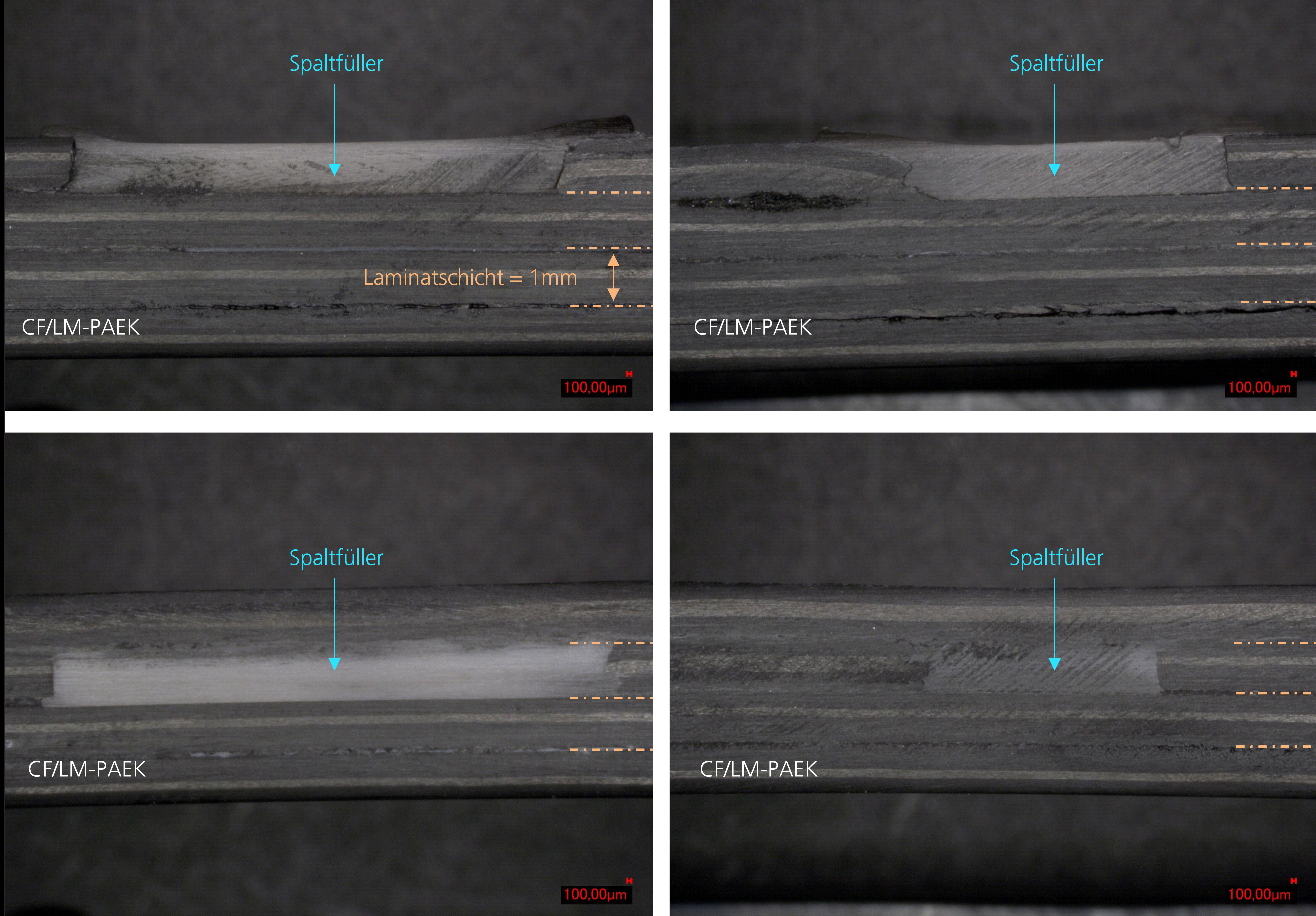
Das vom Fraunhofer IFAM in Stade entwickelte automatisierte Spaltfüllverfahren ermöglicht es, beim Fügen von Bauteilen verbleibende Spalte mit variablen Breiten schnell und präzise zu verschließen. Dadurch werden Gas- und Feuchtigkeitseinschlüsse vermieden. Ein robotischer Endeffektor mit Extruder wird entlang des Spalts geführt und appliziert dabei präzise den schmelzflüssigen Kunststoff in den zuvor vom Endeffektor-Sensor geometrisch vermessenen Spalt. Für die ausreichende Haftung des Füllmaterials erfolgt unmittelbar vor der Applikation eine thermische Vorbehandlung der thermoplastischen Kontaktflächen.
Werden einzelne Faserverbundbauteile miteinander zu einer Gesamtstruktur gefügt, treten fertigungs- und montagebedingt Spalte und Fugen (sogenannte »Gaps«) variierender Breite und Länge auf. Solche Spalte lassen Feuchtigkeit und Gase ein- bzw. austreten, was zu Korrosion und Beeinträchtigung der Strukturfestigkeit führen kann. Besonders in der Luftfahrt und Raumfahrt, aber auch bei maritimen Anwendungen, wie im Schiffsbau, müssen Fügestellen dicht gegenüber Feuchtigkeit und Gasen sein.
Dichten bei duroplastischen FVK
Je nach Fügeverfahren und nachgelagerter Bearbeitung werden Spalte und Fugen heutzutage mit gängigen Dichtstoffen gefüllt bzw. versiegelt. Bei diesen Dichtstoffen handelt es sich meist um Epoxide, Polyurethane, MS-Polymere, Polysulfide und Silikone, die für Faserverbundkunststoffe (FVK) mit duroplastischer Matrix von Bedeutung sind. Seit einigen Jahren werden jedoch Produkte und Strukturen mit thermoplastischer Matrix zunehmend in größeren Industriezweigen, wie in der Automobilindustrie und insbesondere auch in der Flugzeugproduktion, eingesetzt.
Automatisiertes Dichten mit Hochleistungskunststoffen l thermoplastischen Dichtstoffen
Allerdings ist der Einsatz gängiger Dichtstoffe üblicherweise bei thermoplastischer Matrix nicht unmittelbar möglich. Aufgrund der niedrigen Oberflächenenergie sowie Apolarität einiger technisch und wirtschaftlich bedeutsamer Thermoplaste ist für eine ausreichende Anbindung zwischen Dichtstoff und Bauteiloberfläche eine bestimmte Vorbehandlung nötig. Zudem sind die meisten Dicht- und Fugenfüllstoffe für nachgelagerte Bearbeitungen – wie z.B. Thermoplast-Schweißen – ungeeignet, da sie besonders auf Hochleistungsthermoplasten keine ausreichende Beständigkeit gegenüber den hohen Prozess- und Bearbeitungstemperaturen aufweisen.
Hier ist die Anwendung von thermoplastischem Versiegelungsmaterial von besonderer Bedeutung. Für die Materialverträglichkeit während der Bearbeitung wird bestenfalls sogar dasselbe Material zum Füllen verwendet, in das auch die Fasern des Faserverbundbauteils eingebettet sind.
Für das Spaltfüllen (»Gap-filling«) und Versiegeln mittels thermoplastischer Kunststoffe steht dem Fraunhofer IFAM in Stade ein Extruderwerkzeug zur Verfügung. Zur Füllung von Spalten unterschiedlicher Größe wird der Extruder mit einer speziell angepassten Düse ausgestattet. Für die Bestimmung der Spaltgeometrie auch während des Prozesses verfügt das Werkzeug über einen 2D-Linienscanner. Durch die intelligente Kommunikation zwischen Mess-Sensorik und Extruder ist ein volumengenaues und überschussfreies Füllen von Spalten möglich. Der Extruder erlaubt die Verarbeitung von Kunststoffen wie PA, PMMA, PPS bis hin zu Hochleistungskunststoffen wie PEEK oder LMPAEK. Dabei lässt sich neben dem reinen Kunststoffgranulat auch faserhaltiges Granulat verarbeiten.
Das Extruderwerkzeug kann an einen Industrieroboter angekoppelt und von ihm geführt werden. Es ermöglicht somit auch die präzise automatisierte Spaltfüllung bei komplex geformten Bauteilen bis hin zu Großstrukturen.
Unterschiedliche Anforderungen bei der Füllung und Versiegelung an thermoplastischen (Faserverbund-) Strukturen erfordern oft die Entwicklung individueller Lösungen. Deshalb sind sowohl die Beratung des Anwenders, die Auswahl und Charakterisierung des Spaltfüll- und Versiegelungsmaterials als auch die geeignete Auswahl oder Entwicklung von Endeffektor- und Düsensystemen bis hin zur Applikationstechnik Teil der FuE-Arbeiten am Fraunhofer IFAM in Stade. Auf dieser Grundlage können komplette kundenspezifische Spaltfüll- und Versiegelungsprozesse ausgelegt werden.
Die Forschungs- und Entwicklungsarbeiten zur automatisierten Spaltfülltechnologie gehören zu dem FuE-Tätigkeitsfeld Automatisierung und Produktionstechnik des Fraunhofer IFAM. Das Team der Abteilung »Fügetechnologien« verfügt über eine robotergestützte Anlage zum Spaltfüllen mittels unterschiedlicher Endeffektoren. Anwendungsfelder sind bisher das Füllen von Spalten an duroplastischen FVK-Strukturen sowie das Versiegeln von Spalten an den Fügestellen von Schalenelementen von thermoplastischen FVK-Flugzeugrumpfschalen.